Polymers are produced by combining a large number of small molecular units (monomers) by the chemical process known as polymerisation to form long-chain molecules. There are two main types. Thermoplastics consist of a series of long-chain polymerised molecules, in which all the chains are separate and can slide over one another. In thermosetting polymers the chains become cross-linked so that a solid material is produced that cannot be softened and that will not flow.
Polymers are usually made in one of two polymerisation processes. In condensation-polymerisation the linking of molecules creates by-products, usually water, nitrogen or hydrogen gas. In addition-polymerisation no by-products are created. Both thermosetting and thermoplastic polymers can be manufactured by these processes.
Types of Polymers
Thermoplastic Polymers
The long-chain molecules of a thermoplastic polymer are held together by relatively weak van der Waals forces, but the chemical bonds along the chain are extremely strong (Fig. 1a) When the material is heated, the intermolecular forces are weakened and the polymer becomes soft and flexible; at high temperatures it becomes a viscous melt. When it is allowed to cool again it solidifies.
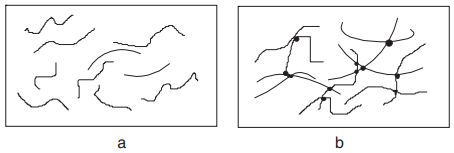
thermoplastic polymer; (b), the attached and/or
cross-linked molecules of a thermosetting polymer.
The cycle of softening by heating and hardening by cooling can be repeated almost indefinitely, but with each cycle the material tends to become more brittle. Thermoplastic materials can have either a semicrystalline ordered structure or an amorphous random structure.
Civil engineering materials such as polypropylene, nylon 66 and polycarbonate are examples of amorphous thermoplastic polymers. Developments in the field of engineering polymers include the introduction of high-performance polymers, such as polyethersulphone (PES), which is amorphous, and polyetheretherketone (PEEK), which is semicrystalline; these polymers offer properties far superior to those of the normal thermoplastic polymers. They are not normally employed in civil engineering owing to their high costs but they are used in the aerospace engineering industry.
Thermosetting Polymers
The principal thermosetting polymers that are used in construction are polyesters, vinylesters and epoxies. They may be used for two different functions: firstly as a composite when combined with a fibrous material and secondly as an adhesive; in the latter case epoxies are generally used.
Thermosetting polymers are formed in a two-stage chemical reaction when a polymer (e.g. polyester, vinylester or epoxy) is reacted with a curing agent (e.g. triethylenetetramine (TETA)). Firstly, a substance consisting of a series of long-chain polymerised molecules, similar to those in thermoplastics, is produced, then the chains become cross-linked. This reaction can take place either at room temperature or under the application of heat and pressure.
As the cross-linking is by strong chemical bonds, thermosetting polymers are rigid materials and their mechanical properties are affected by heat. Two basic procedures are employed to polymerise the thermosetting polymers used in the civil engineering industry; these are the cold-cure systems that are cured at ambient temperatures and the hot-cure systems, in which the polymerisation is performed at elevated temperatures.
Thus different resin and curing systems are required for site and factory manufacture of FRP composites (e.g. the coldcure systems for site work and the hot-cure systems for factory fabrication). Consideration must be given to the glass transition temperature, Tg, of cold-cure epoxy polymers.
Foamed Polymers
A rigid foam is a two-phase system of gas dispersed in solid polymer, and is produced by adding a blowing agent to molten resin. In the exothermic polymerisation reaction the gas is released and causes the polymer to expand, increasing its original volume many times by the formation of small gas cells. Like solid polymers, rigid foam polymers can be either thermoplastic or thermosetting and generally any polymer can be foamed.
Processing of Thermoplastic Polymers
Thermoplastic polymers may readily be processed into sheets or rods or complex shapes in one operation, which is often automated. Stages such as heating, shaping and cooling will ideally be a single event or a repeated cycle. The principal processing methods are extrusion, injection moulding, thermoforming and calendering.
The first is the most important method from the civil engineering viewpoint, and this is therefore outlined below. Powder or granules of thermoplastic polymer are fed from a hopper to a rotating screw inside a heated barrel; the screw depth is reduced along the barrel so that the material is compacted. At the end of the barrel the melt passes through a die to produce the desired finished article. Changing the die allows a wide range of products to be made, such as:
- profile products
- film-blown plastic sheet
- blow-moulded hollow plastic articles
- co-extruded items
- highly orientated grid sheets.
Profile Products
With different extrusion dies, many profiles can be manufactured, such as edging strips, pipes, window-frames, etc. However, success depends upon the correct design of the die.
Film-blown Plastic Sheet
Molten plastic from the extruder passes through an annular die to form a thin tube; a supply of air inside the tube prevents collapse and when the film is cooled it passes through collapsing guides and nip rolls and is stored on drums. Biaxial orientation of the molecules of the polymer can be achieved by varying the air pressure in the polymer tube, which in turn controls the circumferential orientation. Longitudinal orientation can be achieved by varying the relative speeds of the nip roll and the linear velocity of the bubble; this is known as draw-down.
Blow-moulded Hollow Plastic Articles
A molten polymer tube, the Parison, is extruded through an annular die. A mould closes round the Parison and internal pressure forces the polymer against the sides of the mould. This method is used to form such articles as bottles and cold-water storage tanks. The materials commonly used are polypropylene, polyethylene and polyethylene terephthalate (PET).
Co-extruded Items
A multilayered plastic composite is sometimes needed to withstand the end use requirements. Two or more polymers are combined in a single process by film blowing with an adhesive film between them. Reactive bonding processes to chemically cross-link the polymers are under development.
Highly Orientated Grid Sheets
Polymer grids are used in civil engineering as the reinforcement for soil in reinforced earth. Continuous sheets of thermoplastic polymers, generally polypropylene or polyethylene, are extruded to very fine tolerances and with a controlled structure. A pattern of holes is stamped out in the sheet and the stampings are saved for re-use.
The perforated sheet is stretched in the longitudinal and then in the transverse direction to give a highly orientated polymer in the two directions, with a tensile strength similar to that of mild steel. The low original stiffness of the material can be increased ten-fold. The stiffness of unorientated high-density polyethylene (HDPE), for instance, is initially only 1 GPa, but after forming into an orientated molecular structure it increases to 10 GPa.
In injection moulding, softened thermoplastic polymer is forced through a nozzle into a clamped cold mould. When the plastic becomes cold, the mould is opened and the article is ejected; the operation is then repeated.