A composite material is made by combining two or more materials that are mutually insoluble by mixing or bonding them in such a way that each maintains its integrity. Some composites, plastics modified by adding rubber particles, plastics reinforced by chopped glass fibers, cemented carbides, and concrete. These and many other composite materials consist of a matrix of one material that surrounds particles or fibers of a second material, as shown in Fig. 1.
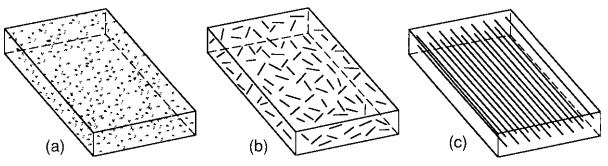
Some composites involve layers of different materials, and the individual layers may themselves be composites. Materials that are melted (alloyed) together are not considered composites, even if a two-phase structure results, nor are solid solutions or precipitate structures arising from solid solutions. Some representative types and examples of composite materials and their uses are listed in Table 1.
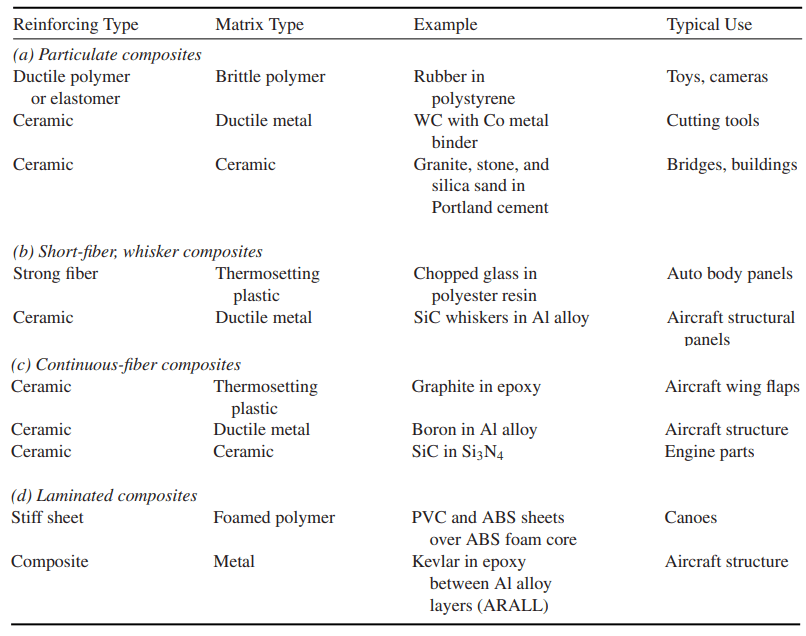
Properties and Applications of Composite Material
Materials of biological origin are usually composites. Wood contains cellulose fibers surrounded by lignin and hemicellulose, all of which are polymers. Bone is composed of the fibrous protein collagen in a ceramic-like matrix of the crystalline mineral hydroxylapatite, Ca5(PO4)3OH.
Composite materials have a wide range of uses, and their use is rapidly increasing. Man-made composites can be tailored to meet special needs such as high strength and stiffness combined with light weight. The resulting high-performance (and expensive) materials are increasingly being used in aircraft, space, and defense applications, and also for high-grade sports equipment, as in golf club shafts and fishing rods.
More economical composites, such as glass-reinforced plastics, are continually finding new uses in a wide range of products, such as automotive components, boat hulls, sports equipment, and furniture. Wood and concrete, of course, continue to be major construction materials, and new composites involving these and other materials have also come into recent use in the construction industry.
Various classes of composite materials will now be discussed.
Particulate Composites
Particles can have various effects on a matrix material, depending on the properties of the two constituents. Ductile particles added to a brittle matrix increase the toughness, as cracks have difficulty passing through the particles. An example is rubber-modified polystyrene. Another ductile particle composite made from two polymers is shown broken open in Fig. 2.
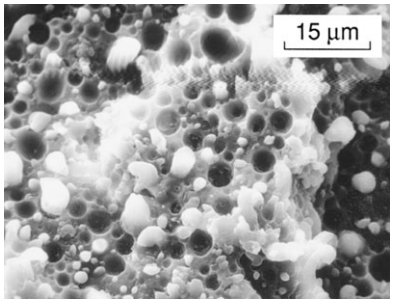
Particles of a hard and stiff (high E) material added to a ductile matrix increase its strength and stiffness. An example is carbon black added to rubber. As might be expected, hard particles generally decrease the fracture toughness of a ductile matrix, and this limits the usefulness of some composites of this type.
However, the composite may still be useful if it has other desirable properties that outweigh the disadvantages of limited toughness, such as the high hardness and wear resistance of cemented carbides.
If the hard particles in a ductile matrix are quite small and limited in quantity, the reduction in toughness is modest. In a metal matrix, a desirable strengthening effect similar to that of precipitation hardening can be achieved by sintering the metal in powder form with ceramic particles of size on the order of 0.1μm. This is called dispersion hardening. The volume fraction of particles seldom exceeds 15%, and the amount may be as small as 1%.
Aluminum reinforced in this manner with Al2O3 has improved creep resistance. Tungsten is similarly dispersion hardened with small amounts of oxide ceramics, such as ThO2, Al2O3, SiO2, and K2O, so that it has sufficient creep resistance for use in lightbulb filaments. Note that particles introduced in this manner will not have a coherent crystal structure with the parent material.
Fibrous Composites
Strong and stiff fibers can be made from ceramic materials that are difficult to use as structural materials in bulk form, such as glass, graphite (carbon), boron, and silicon carbide (SiC). When these are embedded in a matrix of a ductile material, such as a polymer or a metal, the resulting composite can be strong, stiff, and tough.
The fibers carry most of the stress, whereas the matrix holds them in place. Fibers and matrix can be seen in the photograph of a broken open composite material in Fig. 3.
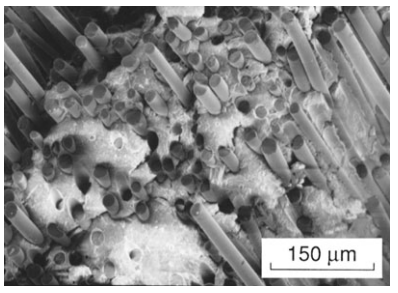
in a CAS glass–ceramic matrix.
Good adhesion between fibers and matrix is important, as this allows the matrix to carry the stress from one fiber to another where a fiber breaks or where one simply ends because of its limited length. Fiber diameters are typically in the size range 1 to 100μm.
Fibers are used in composites in a variety of different configurations, two of which are shown in Fig. 1. Short, randomly oriented fibers result in a composite that has similar properties in all directions. Chopped glass fibers used to reinforce thermoplastics are of this type.
Whiskers are a special class of short fiber that consist of tiny, elongated, single crystals that are very strong because they are dislocation free. Diameters are 1 to 10μm or smaller, and lengths are 10 to 100 times larger than the diameter. For example, randomly oriented SiC whiskers can be used to strengthen and stiffen aluminum alloys.
Long fibers can be woven into a cloth or made into a mat of intertwined strands. Glass fibers in both of these configurations are used with polyester resins to make common fiberglass. High-performance composites are often made by using long, straight, continuous fibers. Continuous fibers all oriented in a single direction provide maximum strength and stiffness parallel to the fibers.
Since such a material is weak if stressed in the transverse direction, several thin layers with different fiber orientations are usually stacked into a laminate, as shown in Fig. 4.
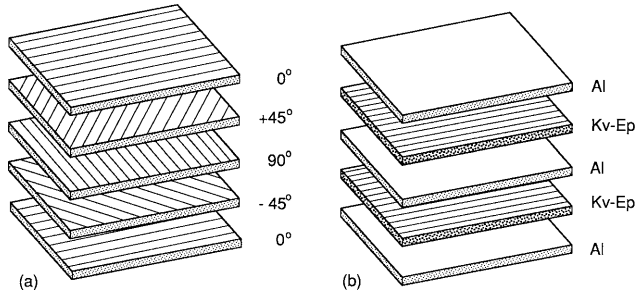
For example, composites with a thermosetting plastic matrix, often epoxy, are assembled in this manner by using partially cured sheets, which are called prepregs because they have been previously impregnated with the epoxy resin.
Appropriate heat and pressure are applied to complete the cross-linking reaction, while at the same time bonding the layers into a solid laminate. Fibers commonly used in this manner with an epoxy matrix include glass, graphite, boron, and the aramid polymer Kevlar. The microstructure of a laminated composite can be seen in Fig. 5.
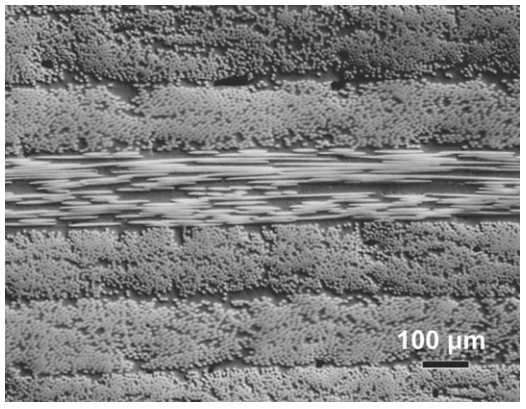
For polymer matrix fibrous composites, strengths comparable to those of structural metals are obtained, as shown in Fig. 6(a). The values for ordinary polyester matrix fiberglass and the lower strength structural metals are similar. But for epoxy reinforced with long fibers of S-glass or graphite, the strength rivals that of the stronger steels. Values of stiffness (E) for high-performance laminates are comparable to those for aluminum, but less than for steel.
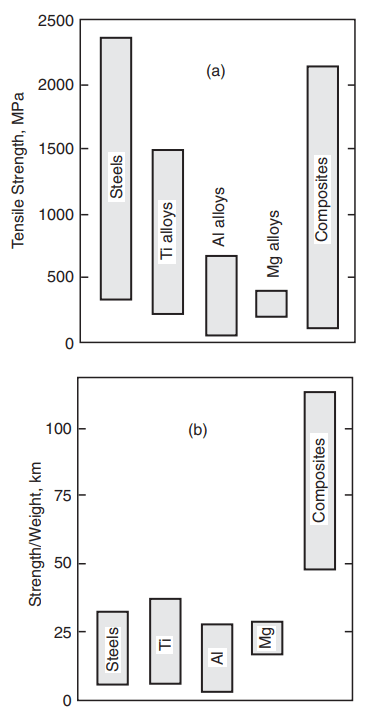
matrix composites, showing ranges for (a) tensile strength, and (b) tensile strength per
unit weight.
However, in considering materials for weight-critical applications such as aircraft structure, it is more relevant to consider the strength-to-weight ratio and the stiffness-to-weight ratio. On this basis, high-performance fibrous composites are superior to structural metals in both strength and stiffness. This is illustrated for strength by Fig. 6(b).
Due to the limitations of the matrix, polymer matrix composites have limited resistance to high temperature. Composites with an aluminum or titanium matrix have reasonable temperature resistance. These metals are sometimes used with continuous straight fibers of silicon carbide of fairly large diameter, around 140μm. Other fiber types and configurations are also used.
For high-temperature applications, ceramic matrix composites have been developed. These materials have a matrix that is already strong and stiff, but which is brittle and has a low fracture toughness. Whiskers or fibers of another ceramic can act to retard cracking by bridging across small cracks that exist and holding them closed so that their growth is retarded. For example, whiskers of SiC in a matrix of Al2O3 are used in this manner. Continuous fibers can also be used, such as SiC fibers in a matrix of Si3N4.
Some intermetallic compounds, such as Ti3Al and NiAl, have ceramiclike properties, but also a helpful degree of ductility at high temperature that encourages their use as matrix materials for temperature-resistant composites.
Laminated Composites
A material made by combining layers is called a laminate. The layers may differ as to the fiber orientation, or they may consist of different materials. Plywood is a familiar example of a laminate, the layers differing as to grain direction and perhaps also as to type of wood. As already noted, unidirectional composite sheets are frequently laminated, as in Fig. 4(a). Aramid–aluminum laminate (ARALL) has layers of an aluminum alloy and a composite with unidirectional Kevlar fibers in an epoxy matrix. See Fig. 4(b).
Where stiffness in bending is needed along with light weight, layers of a strong and stiff material may be placed on either side of a lightweight core. Such sandwich materials include aluminum or fibrous composite sheets bonded on each side of a core that is made of a stiff foam. Another possibility is a core made of a honeycomb of aluminum or other material.
Thanks for reading about “properties and applications of composite material”.