Performance of Timber in Fire
The performance of materials in fire is an aspect of durability that has always attracted much attention, not so much from the research scientist, but rather from the material user who has to conform with the legislation on safety and who is influenced by the weight of public opinion on the use of only ‘safe’ materials.
While various tests have been devised to assess the performance of materials in fire there is a fair degree of agreement on the unsatisfactory nature of many of these tests, and an awareness that certain materials can perform better in practice than is indicated by these tests.
Thus, while no one would doubt that timber is a combustible material showing up rather poorly in both the ‘spread of flame’ and ‘heat release’ tests, nevertheless in at least one aspect of performance, namely the maintenance of strength with increasing temperature and time, wood performs better than steel. There is a critical surface temperature below which timber will not ignite. As the surface temperature increases above 100oC, volatile gases begin to be emitted as thermal degradation slowly commences.
However, it is not until the temperature is in excess of 250oC that there is sufficient build-up of these gases to cause ignition of the timber in the presence of a pilot flame. Where this is absent, the surface temperature can rise to about 500oC before the gases become self-igniting. Ignition, however, is related not only to the actual temperature, but also to the time of exposure at that temperature, since ignition is primarily a function of heat flux.
Generally chemical bonds begin to break down at about 175ºC. It is known that the first constituent of timber to degrade is the lignin, and this degradation continues slowly up to 500oC. The hemicelluloses degrade much more quickly between 200 and 260oC, as does the cellulose within the temperature range 260–350oC.
Degradation of the cellulose results in the production of flammable volatile gases and a marked reduction in its degree of polymerisation (chain length) (le Van and Winandy, 1990). The performance of timber at temperatures above ignition level is very similar to that of certain reinforced thermosetting resins that have been used as sacrificial protective coatings on space-return capsules.
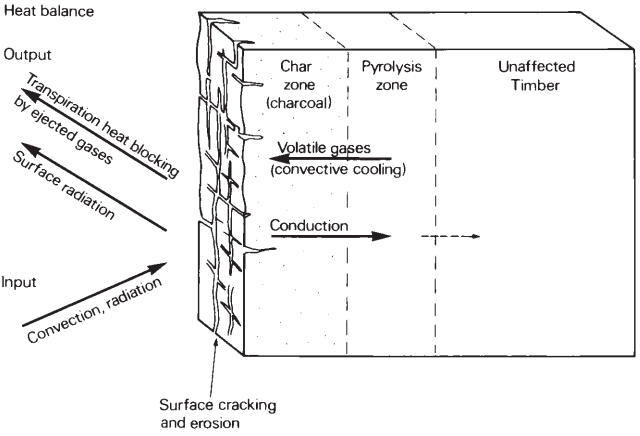
Both timber and these ablative polymers undergo thermal decomposition with subsequent removal of mass, leaving behind sufficient residue to protect the residual material. The onset of pyrolysis in timber is marked by a darkening of the timber and the commencement of emission of volatile gases; the reaction becomes exothermic and the timber changes to a carbonised char popularly known as charcoal (Fig. 1).
The volatiles, in moving to the surface, cool the char and are subsequently ejected into the boundary layer, where they block the incoming convective heat, a very important phenomenon known as transpirational cooling. High surface temperatures are reached and some heat is emitted by thermal radiation; the heat balance is indicated in Fig. 1.
The surface layers crack badly both along and across the grain and surface material is continually, but slowly, being lost. A quasi-steady state is reached, therefore, with a balance between the rate of loss of surface and the rate of recession of the undamaged wood. The rate at which the front recedes is a product of:
- the heat flux
- the temperature of combustion
- the oxygen level.
In the UK, evidence has been produced (Hall and Jackman, 1975) that demonstrates that under exposure to a fully developed fire as represented by the fire resistance test (BS 476: Part 8: now withdrawn) the surface of large softwood and mediumdensity hardwood timber sections recedes at a rate of approximately 0.64 mm/min.
For high-density hardwoods of an equivalent size, the value is given as 0.5 mm/min. In mainland Europe, where furnaces are fuelled by oil, which provides a greater radiant component to the flames from the burners that are used to heat the furnace, they have used higher softwood charring rates, e.g. 0.8 mm/min. The values set out in Eurocode 5: Part 1–2 (BS EN 1995-1-2): General Rules – Structural Fire Design for timber of a stated minimum dimension reflect mainland Europe’s experience and should be used in all calculations.
It should be appreciated that small sections of timber will always char at an enhanced rate, and caution must be exercised when applying the Eurocode rates to smaller sections. The formation of the char protects the unburnt timber, which may be only a few millimetres from the surface. Failure of the beam or strut will occur only when the cross-sectional area of the unburnt core becomes too small to support any static or dynamic load.
By increasing the dimensions of the timber above those required for structural considerations, it is possible to guarantee structural stability and/or load-bearing capacity in a fire for a given period of time. This is a much more desirable situation than that presented by steel, where total collapse of the beam or strut occurs at a critical temperature that is proportional to the stress in the member.
Methods of Assessing Reaction to Fire of Constructional Materials
The formation of the European Community (EC) as a free trade area and the production of the Construction Products Directive (CPD) led automatically to the introduction and implementation of new European standards that would allow products manufactured in one country in the EC to be used in all the other countries of the EC. With reference to the reaction to fire of constructional materials, EN 13501-1 classifies all constructional products into one of six Euroclasses (A–F) according to their reaction-to-fire performance in fire tests.
Two of these tests classify the least combustible materials (Euroclasses A1 and A2); these two new tests are a small furnace test for non-combustibility (EN ISO 1182) and an oxygen bomb calorimeter test, which measures the heat of combustion of the material (EN ISO 1716). At the lower end of the range of Euroclasses (classes E and F), construction products of appreciable combustibility will be assessed using a simple ignitability test (EN ISO 11925-2).
Products that fall into Classes A2, B1 C and D (and D contains timber and wood-based panels) will be tested using the single burning item test (EN ISO13823), except where the products are used as floor coverings, for which the critical flux (radiant panel) test (EN ISO 9239-1) will be used to determine performance in Euroclasses B–E. For both floor and non-floor applications, generally only two of the above tests will be required to characterise the performance of any one product.
The UK position in late 2008: Appendix A to both volumes of Approved Document B (Fire Safety) of the Building Regulations (dwelling houses and other buildings) sets out the recommendations in England and Wales for the fire performance of materials, products and structures using two alternative systems, one of which utilises EN standards, while the second continues to permit the use of national (British) standards. Similar dual systems apply to Scotland and Northern Ireland.
In the section relating to the reaction to fire of non-combustible materials, performance is defined in terms of National classes (clause 8a), defined by testing to BS 476-4:1970 (non-combustible test for materials) or BS 476-11:1982 (method for assessing the heat emission from building products), or European classes (clause 8b) as class A1 in accordance with BS EN 13501-1 and when tested to BS EN ISO 1182 and BS EN ISO 1716.
For materials of limited combustibility (which includes timber and panel products), performance is again defined in terms of National classes (clause 9a) using the method specified in BS 476-11:1982 or in terms of European classes when classified as class A2-s3,d2 in accordance with BS EN 13501-1 when tested to BS EN ISO1182 or BS EN ISO 1716. A similar picture relates to wall linings, for which where national or European standards may be used. The relevant national standards are BS 476- 7:1997 and BS 476-6:1989.
The most commonly recommended rating, class 1, used for the majority of rooms and circulation spaces, is proven by testing the lining (including the substrate) to BS 476-7: 1997. Should the circulation space form part of the dedicated escape route from the building, then the lining must also be tested by the method described in BS 476-6: 1989, ‘the fire propagation test’, and satisfy the criteria given in the approved document or other guidance documents. Materials meeting the dual requirement are known as class ‘0’ materials. Small rooms in both dwellings and other buildings (as defined in the guidance) are permitted to be lined with class 3 materials as determined by BS 476-7.
Timber in its undecorated state is assumed to be class 3, but by treatment can be made to meet both class 1 and class 0 criteria (see section 56.3.1, Flame retardants). The relevant European standard is BS EN 13501-1. For the majority of rooms and circulation areas, lining materials must have a rating of C-s3,d2, while for circulation areas that form part of the dedicated escape route, the lining must have a B-s3,d2 classification, and for small residential rooms of less than 4 m2 , a lining having a lower classification of D-s3,d2 may be used.
When the classification includes ‘s3,d2’ this means that there is no limit set for smoke production and/or flaming droplets or particles. Further information and guidance on the use of the dual system is given in BS 476-10, published 2008.
The use of national and CEN standards: The inclusion of certain parts of BS 476 in approved documents B of the UK Building Regulations means that products manufactured abroad (excluding the other CEN countries) and tested to the relevant parts of BS 476 according to Appendix A of approved document B may be used in construction within the UK.
A further consequence of this inclusion is that a UK manufacturer can have his product certified to BS 476 for its use in construction solely in the UK rather than employing the more costly route through EN certification. Products manufactured in Europe, or elsewhere in the world when tested in accordance with the relevant reaction to fire ENs (as of 2008) have free access to the UK market in building construction, owing to the dual system in the guidance documents for the UK building regulations.
The above reaction-to-fire tests relate to the material or product. When that product is incorporated into a building element, the fire resistance of that element will be determined by a whole series of other tests.