In this aritcle, we will briefly discuss some alternatives to Portland cement. These include calcium aluminate cement, which has been in use for a hundred years or so, and some cements that have had more limited use or are currently being developed and are not yet in widespread use.
This latter group is of particular interest because of their potential of being produced at lower temperatures than Portland cement, thereby requiring less energy for production; this is a major concern for Portland cement in relation to sustainability issues, particularly carbon emissions.
Calcium Aluminate Cement
Calcium aluminate cement (CAC) is, as can be deduced from the name, based on calcium aluminate rather than the calcium silicate of Portland cement. It is also known as high-alumina cement (HAC); the two names are synonymous. It was first developed in France in the early years of the 20th century to overcome the problem of sulphate attack that was being experienced by Portland cement concrete. Its French name is Ciment Fondu, and supplies in Europe are covered by BS EN 14647.
Manufacture and composition: The manufacture of CAC has some parallels with that of Portland cement. The raw materials are usually limestone and bauxite, which contains alumina (aluminium oxide), iron and titanium oxides and some silica. After crushing and blending these are fed into a furnace and heated to about 1600°C, where they fuse into a molten material.
This is drawn off, cooled and ground to the required particle size, which is normally of the same order as that of Portland cement, i.e. a specific service area of 290 to 350 m2 /kg. The relative particle density is 3.20, marginally higher than that of Portland cement (3.15), and the powder is very dark grey owing mainly to the significant amounts of iron oxide usually present in the bauxite, but if a white bauxite with little or no iron oxide is used then the cement is light grey to white.
The oxide proportions are typically 35 – 40% each of alumina (Al2O3 or A in shorthand form) and lime (CaO or C), about 15% iron oxides (Fe2O3 or F), about 5% of silica (SiO2 or S) and some other minor compound present in the raw materials. The principal cementitious compound is CA, with some C12A7, C2S and C2AS and C6A4FS.
Hydration and conversion: The setting time of CAC is about 30 minutes longer than that of a typical Portland cement. At temperatures up to about 35°C the first hydration reaction is simply:
CA + 10H → CA.10H
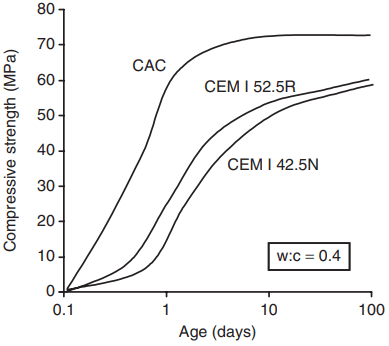
This reaction is relatively rapid and gives rise to an initial rate of strength gain much greater than that of Portland cements (Fig. 1), but as with Portland cement the hydration reaction is exothermic and consequently there is a more rapid rate of heat evolution. Between 35 and 65°C the dominant hydration reaction is:
2CA + 11H → C2A.8H + A.3H and above 65°C it is:
3CA + 12H → C3A.6H + 2A.3H
The products of this last reaction are in fact stable at all temperatures, whereas those of the first two reactions are metastable, and with time will transform or convert to the stable phases:
2CA.10H → C2A.8H + A.3H + 9H
3C2A.8H → 2C3A.6H + A.3H + 9H
The rate of conversion is temperature dependent, and takes years to complete at 20°C but only days at 60°C (Fig. 2).
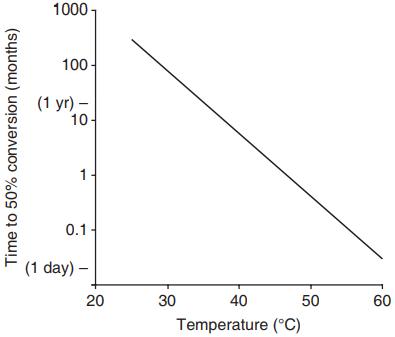
conversion of CAC concrete (after Neville, 1995).
A major consequence of conversion arises from the solid density of the final stable product (C3A.6H) being greater than that of the metastable products of reactions (16.1) and (16.2). Hardened cement that has been formed at low temperatures will therefore become more porous as its hydrates convert, with a consequent loss of strength. This loss can occur at any time in the life of the concrete in the event of an increase in temperature, as shown in Fig. 3.
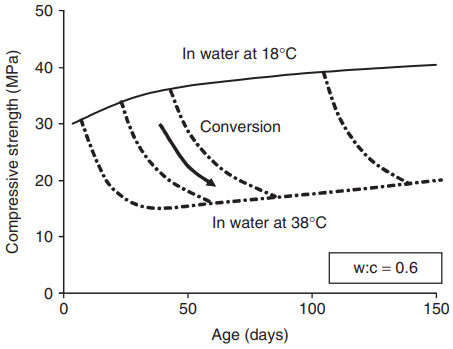
conversion.
An essential feature of the conversion is that it does not result in disintegration of the concrete and the products have a significant and stable strength, albeit lower than that of the initial hydrates. The strength – both before and after conversion – depends on the initial water:cement ratio, as shown in Fig. 16.4.
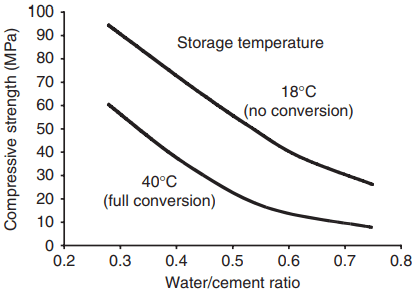
strength of CAC concrete stored for 100 days at two
temperatures.
Uses: As mentioned above the initial uses of CAC concrete were to provide sulphate resistance. However the rapid rate of strength gain made it particularly suitable for the production of pre-cast pre-stressed concrete beams that could be demoulded a few hours after casting and placed in service within a few days. These beams were a feature of the new and high-rise building construction in the period following the Second World War.
Conversion was known about at this time, but it was not thought to be significant if section sizes were limited to avoid high temperatures from the exothermic hydration reactions, the water:cement ratio was limited to a maximum of 0.5 and warm moist service environments were avoided.
However, a number of failures of ceilings and roofs constructed with CAC beams occurred in the UK in the 1970s. Fortunately none of these involved loss of life but subsequent investigations found significant conversion of the CAC. However the primary causes of failures were identified as design and tolerance problems, particularly relating to the bearing area and structural link provided between the beams and their support walls.
Subsequent inspection of more than a thousand buildings containing CAC concrete found only one case of a problem attributed to strength loss during conversion. Despite this CAC was omitted from the list of cements permitted in design standards for reinforced and pre-stressed concrete, and so it was effectively banned from use for this purpose in the UK and in many other countries.
Further problems involving similar CAC beams occurred in some Spanish apartment blocks in the 1990s, including one collapse; the concrete was found to have disintegrated owing to its high porosity and the use of poor quality aggregates, indicating the importance of understanding the complexity of the materials issues involved. Two recent papers (Neville, 2009) have discussed the background to the original failures, the investigation that followed and its consequences; they make interesting reading.
A Concrete Society report (Concrete Society, 1997) concluded that in some circumstances CAC concrete could be safely used if its long-term strength is taken into account for design purposes, but there has been no inclusion of this provision in UK or European codes of practice.
There are, however, several current important uses of CAC cement and concrete that take advantage of its superior properties compared to other cements:
- Its excellent resistance to acids, particularly those derived from bacteria, means that it is ideal for use for tunnel linings and pipes in sewage networks.
- Its rapid strength gain lends itself to uses in applications where rapid service use is required, such as temporary tunnel linings; blends of CAC and ggbs have been used for this purpose.
- Its strength and hard-wearing characteristics make it useful in non-structural finishing operations such as floor levelling, and in mortars for fixing and rapid repairs. In these materials mixed binders of CAC, Portland cement and calcium sulphate are often used.
- CAC concrete has excellent resistance to high temperatures and thermal shock and so it is used in foundry floors and in refractory bricks for furnace linings.
Alkali-activated Cements
These are cements in which materials that are not cementitious in themselves, or are only weakly so, such as the Type 2 additions, are activated by alkalis to form cementitious compounds. These are generally calcium silicate hydrates as in hardened Portland cement.
A number of strong alkalis or salts derived from them can be used, including caustic soda (sodium hydroxide, NaOH), soda ash (sodium carbonate, Na2CO3), sodium silicates (a range of compounds with the general formula Na2O, nSiO2) and sodium sulphate (Na2SO4). The cementing components include:
- slags such as ground granulated blast furnace slag, granulated phosphorus slag, steel slag (from the basic oxygen or electric arc process, all of which should be rapidly cooled to give an unstable or active microstructure
- pozzolans such as volcanic ash, fly ash, metakaolin and condensed silica fume; these are often mixed with lime as well as the activator.
There is thus a considerable number of possible combinations of activator and cementing compound, with slag activated by sodium hydroxide, sodium carbonate or sodium silicates having been widely studied and used for concrete, primarily in Eastern Europe and China.
Although the resulting concretes obey the same or similar rules to Portland cement concrete, such as the influence of water:cement ratio on strength, and can achieve similar mechanical properties, they are not without their problems, such as high drying shrinkage, variability of the raw materials and inadequate understanding of long-term properties.
Also, some of the activators, particularly sodium hydroxide, are corrosive and require very careful handling. We do not have room to describe these in any detail here, but if you are feeling confident, a comprehensive treatment has been produced by Shi et al. (2006).
Geopolymer Cements
This is the name for a group of cements that are produced from alumina- and silica-containing raw materials. These are transformed into silico-aluminates by heating to relatively low temperatures (about 750°C). The silico-aluminates have a ring polymer structure, hence the name ‘geo-polymer’; the more specific name polysialates has also been suggested (Davidovits, 2002).
These compounds have some cementitious properties but if they are blended with an alkali-silicate activator and ground blast furnace slag the resulting cement has accelerated setting time and a high rate of strength gain (up to 20 MPa after four hours at 20°C) as well as high longer term strength (more than 70–100 MPa at 28 days). There are therefore some similarities with the alkali activated cements discussed above.
These properties are very useful for repair concrete, for example for roads and runways. Blends with Portland cement are also used.
Magnesium Oxide-based Cements
These can be derived from:
- Magnesium carbonate. On heating to about 650°C magnesium carbonate dissociates to reactive magnesium oxide (magnesia). This is mixed with Portland cement and other industrial by-products such as slag or fly ash to form the binder (Teccement, 2009). During hydration the magnesia forms magnesium hydroxide (brucite), which has some cementitious properties in itself, but which may also enhance the hydration of the Portland cement.
- Magnesium silicate. This decomposes at about 650°C yielding a cementitious product. The process is being developed and the resulting cement investigated (Novacem, 2009), but so far little information and few results have been published.
Waste-derived Cements
The search for uses of industrial waste as an alternative to sending it to landfill has resulted in the development of some potential processes for conversion to cementitious materials. In Japan an ‘Ecocement’ has been produced in which up to 50% of the raw materials for Portland cement production is substituted by municipal solid waste in the form of incinerator ash and sewage sludge (Shimoda and Yokoyama, 1999).
The required clinkering temperature (1350°C) is a little lower than that for Portland cement (1450°C); the resulting cement contains similar compounds to Portland cement albeit with a generally higher C3A content. Its properties are, not surprisingly, claimed to be similar to those of Portland cement.
However care has to be taken during the production process to remove and recover chlorides and toxic heavy metals. A rapid-hardening version in which the chlorides are not recovered is also available. In the UK a process has been developed that involves blending a variety of industrial waste products and treating these in a low-temperature, low-emission process (Celtic Cement Technology, 2009).
The result is a cement-substitute material which, it is claimed, will outperform blast furnace slag when used as an addition to Portland cement. Altering the combination of waste and the particle size distribution gives products with specific compositions for particular applications, for example for concrete with high early or high long-term strength or fast or slow setting.