A wide variety of tensile behaviors occur for different materials. Even for a given chemical composition of a material, the prior processing of the material may have substantial effects on the tensile properties, as may the temperature and strain rate of the test.
Trends for Different Materials
Engineering metals vary widely as to their strength and ductility. This is evident from Table 1, where engineering properties from tension tests are given for a number of metals.
Relatively high strength polymers in bulk form are typically only 10% as strong as engineering metals, and their elastic moduli are typically only 3% as large. Their ductilities vary quite widely, some being quite brittle and others quite ductile. Properties of some commercial polymers are given in Table 2 to illustrate these trends.
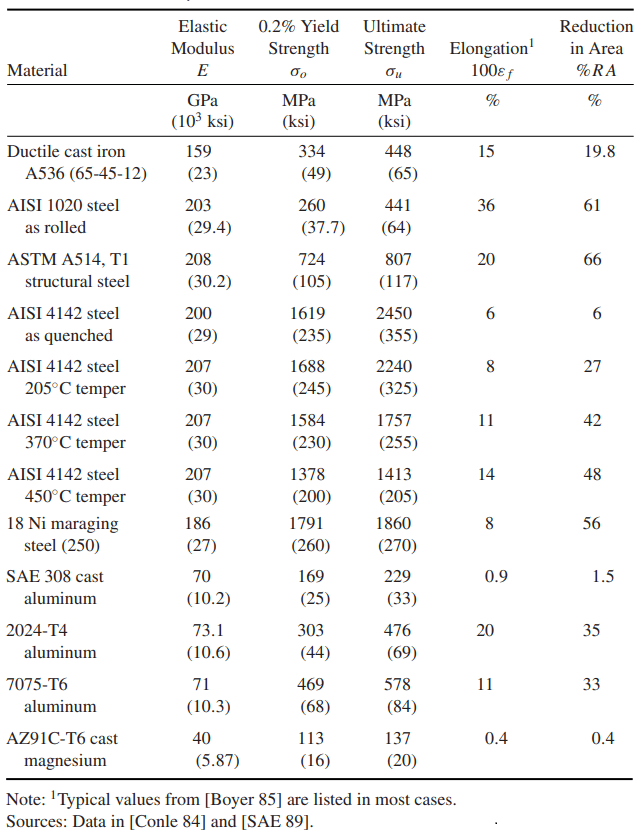
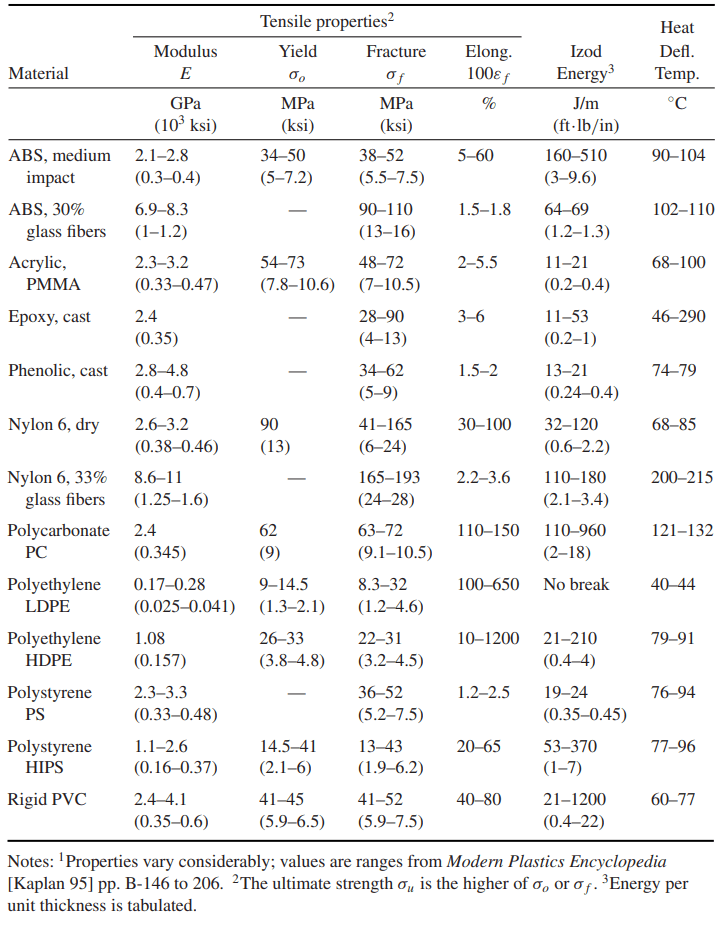
Rubber and rubber-like polymers (elastomers) have very low elastic moduli and relatively low strengths, and they often have extreme ductility. Ceramics and glasses represent the opposite case, as their behavior is generally so brittle that measures of ductility have little meaning.
Strengths in tension are generally lower than for metals, but higher than for polymers. The elastic moduli of ceramics are relatively high, often higher than for many metals.
The tensile behavior of composite materials is, of course, strongly affected by the details of the reinforcement. For example, hard particles in a ductile matrix increase stiffness and strength, but decrease ductility, more so for larger volume percentages of reinforcement.
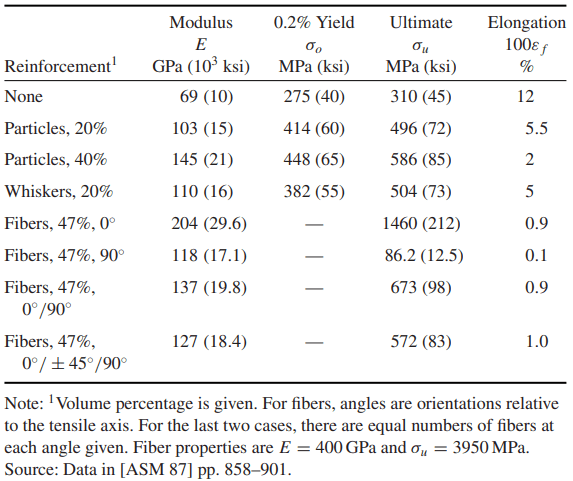
6061-T6 Aluminum Matrix
Long fibers have qualitatively similar effects, with the increase in strength and stiffness being especially large for loading directions parallel to large numbers of fibers. Whiskers and short chopped fibers generally produce effects intermediate between those of particles and long fibers. Some of these trends are evident in Table 3, where data are given for various SiC reinforcements of an aluminum alloy.
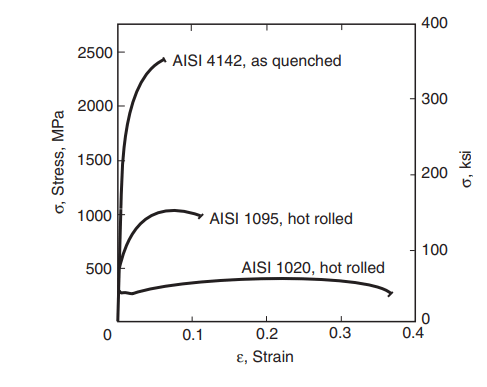
Some stress–strain curves from tension tests of engineering metals are shown in Figs. 1 and 2. The former gives curves for three steels with contrasting behavior, and the latter gives curves for three aluminum alloys.
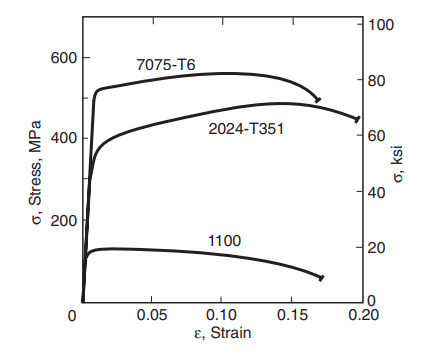
Tensile stress–strain curves for low-ductility metals have only limited curvature and no drop in stress prior to fracture, as for quenched steel in Fig. 1.
Stress–strain curves from tension tests on three ductile polymers are shown in Fig. 3. An early relative maximum in stress is common for polymers, and this is associated with the distinctive necking behavior.
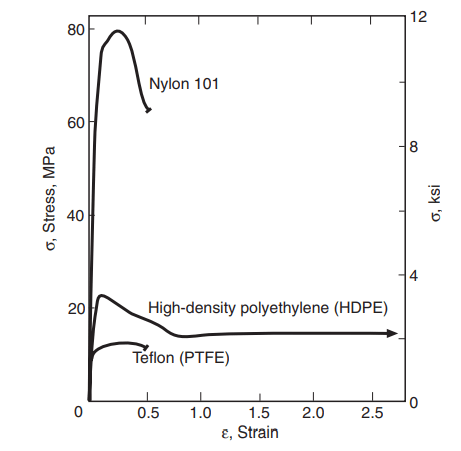
Necking begins when the stress reaches the early relative maximum, and then it spreads along the specimen length, but with the diameter in the neck remaining approximately constant once the process starts.
This behavior is due to the chainlike molecules being drawn out of their original amorphous or crystalline structure into an approximately linear and parallel arrangement.
Other polymers, such as Nylon 101, neck in a manner more similar to metals. An additional type of behavior is seen for Teflon (PTFE). This material deformed a considerable amount by developing a large number of small tears bridged by filaments of material, a process called crazing, followed by failure without necking. Some polymers, such as acrylic (PMMA), behave in a brittle manner and have stress–strain curves that are nearly linear up to the point of fracture.
Ceramics and glass have stress–strain curves with limited curvature, as for low ductility metals, with the curve often being reduced to essentially a straight line terminating at the fracture point.
Effects of Temperature and Strain Rate
If a material is tested in a temperature range where creep occurs—that is, where there is time-dependent deformation—strains from this source will contribute to the inelastic deformation in the test. Moreover, the creep strain that occurs is greater if the speed of the test is slower, as a slower test provides more time for the creep strain to accumulate. Under such circumstances, it is important to run the test at a constant value of strain rate, ε˙ = dε/dt, and to report this value along with the test results.
For metals and ceramics, creep effects become significant around 0.3 to 0.6Tm, where Tm is the absolute melting temperature. Thus, creep strains are a factor at room temperature for metals with low melting temperatures.
Strain rate may also affect the tensile behavior of ceramics at room temperature, but for an entirely different reason unrelated to creep, namely, time-dependent cracking due to the detrimental effects of moisture.
For engineering metals at room temperature, strain-rate effects due to creep exist, but are not dramatic. For example, some data for copper are given in Fig. 4.
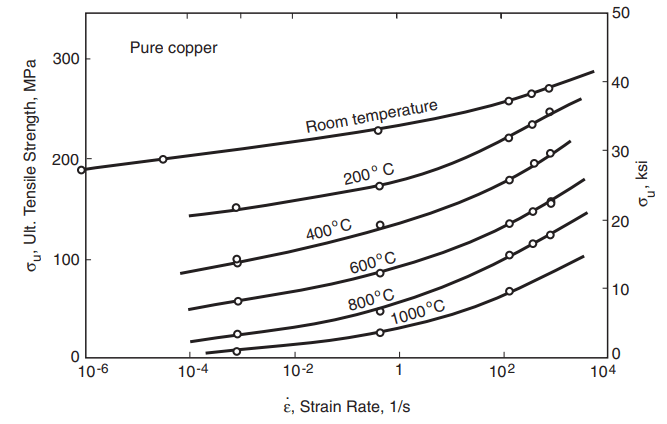
at various temperatures.
In this case, for an increase in strain rate of a factor of 10,000, the ultimate tensile strength at room temperature increases about 14%. Larger relative effects occur at higher temperatures as creep effects become more important. Also, note that the strength is drastically lowered by increased temperature, especially as Tm = 1085◦C is approached.
The following generalizations usually apply to the tensile properties of a given material in a temperature range where creep-related strain-rate effects occur:
- At a given temperature, increasing the strain rate increases the strength, but decreases the ductility.
- For a given strain rate, decreasing the temperature has the same qualitative effects, specifically, increasing the strength, but decreasing the ductility.