Recycling of Bituminous Materials
The recycling and reuse of bituminous materials is not a recent development, the first asphalt pavement recycling project being recorded in 1915 (Epps et al., 1980). Recycled (or reclaimed) asphalt pavement (RAP) material consists of aggregate and bitumen that has been removed and/or reprocessed from an asphalt pavement.
Although old asphalt mixtures were historically removed and disposed of in landfills, the use of RAP in new asphalt mixtures has increased substantially since the 1930s. RAP material is produced when old, damaged pavement materials are milled and crushed for subsequent addition as a component in new asphalt mixtures. With the availability of high-quality virgin materials declining and landfilling becoming less practical and more expensive, the increase in the addition of RAP to pavement mixtures is not surprising.
The benefits of recycling asphalt pavements can be attributed to a reduction in the costs of new construction and rehabilitation projects, environmental conservation of energy, mineral aggregates and bituminous binder, and the preservation of road geometry (Kandhal and Mallick, 1997). Recycling of pavement material can be undertaken as an in-place or a central plant process.
In addition, recycling can be grouped into hot, warm and cold processes depending on the virgin binder deployed in the recycling operation. RAP contents in new asphalt mixtures vary from approximately 10% to as high as 100%, although generally RAP contents of 30% can be considered to be an acceptable maximum (Planche, 2008).
Owing to the benefits of pavement recycling techniques, up to 80% of asphalt pavements removed each year from widening and resurfacing projects are put back into roads, highway shoulders and embankments.
In-plant Asphalt Recycling
In-plant recycling involves stockpiling RAP at the asphalt plant before mixing with virgin material to produce a new asphalt mixture. Reclaimed pavements are transported to the asphalt production plant, ripped, milled, and crushed into required sizes before being blended with virgin bitumen and aggregate. Depending on the mixing temperatures required of the recycled mixture, in-plant recycling is further divided into cold, warm, and hot recycling (Karlson and Isacsson, 2006).
In-plant hot recycling tends to be the most advantageous, hot recycled asphalt mixtures with 10–30% of RAP having a performance that is similar to, or even better than, that of virgin asphalt mixtures (Kandhal and Mallick, 1997).
One of the disadvantages of recycling material in an asphalt plant is the need to transport the RAP material to the plant and the subsequent transport of the recycled asphalt mixture to site. This need for transport results in added expense as well as pavement damage associated with delivery vehicles, which can only be alleviated by an in-situ process.
Hot In-plant Operations
In the hot recycling process, RAP material is blended with superheated virgin aggregate before mixing with virgin bitumen. The role of the superheated aggregate is to transfer heat to the RAP to soften or liquefy the RAP binder and to break the RAP material into smaller lumps. To aid the mixing of the RAP binder with virgin bitumen, rejuvenating agents are also added during the production stage. The role of the rejuvenator is to diffuse into and regenerate the properties of the aged binder. A wide range of rejuvenators – for example, soft bitumens, fluxing oils, extender oils and aromatic oils – can be used (Karlson and Isacsson, 2006).
Batch and drum plants are conventionally used to produce hot asphalt mixtures, but in order to produce hot recycled asphalt mixtures, modifications to the conventional mixing plant are needed (Roberts et al., 1991). In a batch mixing plant, if the RAP material is dried in the same way as the virgin aggregate, the RAP bitumen will be burned directly by the flame in the burner, causing blue smoke.
RAP is therefore stored separately before being introduced to superheated virgin aggregate in the hot bin, the excessive thermal energy being used to heat the RAP material from ambient temperature to mixing temperature. The procedure in the drum facility is quite different from that of the batch plant.
In a conventional drum facility, aggregate is heated and mixed with bitumen in the same drum mixer. The drum facility therefore needs to be modified to incorporate RAP material for the production of hot recycled asphalt mixture.
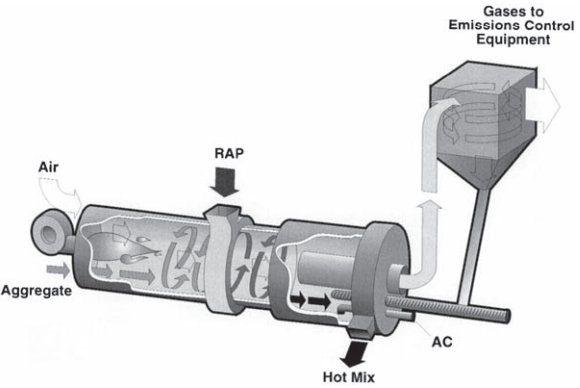
Figure 1 shows a modified drum mixer in which RAP is introduced in the middle section of the drum. The RAP is therefore mixed with superheated virgin aggregate before being mixed with virgin binder.
Cold In-plant Processes
Cold recycled asphalt mixtures are produced using bitumen emulsion rather than conventional bitumen. Cold mixtures have two very significant advantages over hot asphalt mixtures:
- The energy consumption of the plant is typically 10–20% that for hot asphalt mixture production.
- Cold asphalt mixtures can be stored for long periods before use.
The first point leads to clear economic and environmental benefits, offsetting the loss of performance when compared to hot mixtures. The second point means that cold asphalt mixtures make ideal patching and repair materials.
There is a long workability period following placement during which compaction can be achieved, so trench backfills and other small areas of construction can be completed to a high standard. The arrival of cold-mix technology has also spawned a new term, ‘ex-situ’. This refers to the practice of setting up a mobile mixing plant at or near to a work site, which takes recycled materials from the site and incorporates them into a new mixture.
The relative simplicity of cold mix production means that this is an economically attractive option, saving on transport and making re-use of materials practical. In practice cold recycled asphalt mixtures tend to be used almost exclusively on relatively lightly trafficked roads, because of the need for the material to cure and the danger of damage during early life.
In-situ Asphalt Recycling
In-situ methods involve processing on site and are divided into hot in-situ recycling, which includes the remixing and repaving processes, and cold in-situ recycling, which includes full depth reclamation. In-situ recycling is also known as in-place recycling.
Hot In-situ Asphalt Recycling
Hot in-situ asphalt recycling is used to transform an aged and partially failed asphalt surface layer into an as-good-as-new product. The process requires that the surface of the pavement be heated to a temperature at which it can be reworked, healing all cracks and reshaping any deformed profile. This process is usually applicable to depths between 20 and 60 mm.
Repave: In the so-called ‘repave’ process, the uppermost materials are heated to 140–180°C and scarified, i.e. loosened, to a depth of approximately 20 mm before being re-profiled. While the scarified asphalt material is still hot (above approximately 90°C), a new asphalt mixture surfacing layer is laid on top of the old material and both layers are compacted together. The heated old material therefore blends with the new material to form a single contiguous surface course with fully restored properties.
Remix: The remix process is similar to, although slightly more sophisticated than, the repave process. In the remix process, the heated existing surface material is physically scraped up and mixed together with new material in the remixing machine before being re-laid as a new surface layer (Fig. 2).
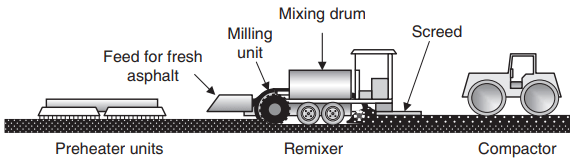
This ensures a fully integrated and blended layer. The bitumen grade and mixture composition of the added material is selected to balance out any defects in the composition of the existing material. The re-mixed material, when compacted, forms a single new 40-mm surface course. This treatment is suitable when the existing surface course has started to deteriorate, by either rutting or cracking, but the underlying layers are still in a sound condition. Limitations are as follows: A fairly consistent existing surface course is necessary.
- A careful mixture design is required to establish the proportions of the added material needed.
- Material deeper than 20 mm below the original pavement surface is not heated sufficiently to be significantly remoulded or improved.
- The process can only be considered as partial recycling because of the need for new material.
- An increased surface level has to be accommodated.
- There is a danger of toxic fumes being emitted during the heating process if it is not carefully controlled.
Both the repave and remix hot recycling processes are excellent in that they transform a failing surface into an intact new layer. However, they have their limitations:
- The existing surface material must be suitably uniform in composition (i.e. not too many patches or other changes of surface material).
- The transformation is only effective to the depth to which the asphalt can be heated. This means that the treatment is ideal as a cure for rutting, top-down cracking or ravelling, but that it does nothing to overcome deeper problems.
Cold In-situ Processes
In full-depth reclamation, the existing pavement (usually all the surface and part of the base) is ripped and milled to a certain depth, which can extend up to 350 mm. The broken fragments are then mixed with a new binder, consisting of bitumen emulsion, foamed bitumen or soft bitumen to produce a stabilised base, and compacted. A new surface is then laid and compacted on the new recycled base (Kandhal and Mallick, 1997).
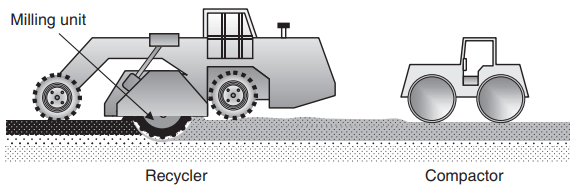
Figure 3 provides an illustration of the process. The result, if design and construction are carried out sensibly, is a strong new pavement, although it will always be necessary to apply a new surface course, since it is unlikely that the requisite surface properties will be present from the recycled material.
There is no need for expensive and disruptive transportation of materials (other than binder) and there is no requirement for quarrying virgin rock. All that is needed is the addition of an effective binder. Naturally there are difficulties, and the following are seen as the major issues confronting practitioners and designers:
- Binder is unlikely to be uniformly mixed into the material.
- All pavements are to a certain extent non-homogeneous, notably in layer thickness. In many cases this means that the milled material will present varying proportions of asphalt, base (including hydraulically-bound materials), subbase and even subgrade.
- Water content can only be controlled approximately.
- Aggregate gradation is likely to be low in fines content if the RAP percentage is high.
- Compaction beyond about 250 mm depth will be increasingly ineffective. Practical advice on cold asphalt recycling can be found in Wirtgen’s Cold Recycling Manual (Wirtgen, 2004).
Issues Related to Asphalt Recycling
Black Rock
If the binder content of the RAP is to be utilised in the final recycled asphalt mixture, then there is a need to activate the binder in the RAP. It will usually have aged over a period of many years and will therefore be much harder than new bitumen or bitumen emulsion. RAP in this state is often referred to as ‘black rock’.
Nevertheless, with appropriate addition of chemical rejuvenators it has been shown that it is possible to induce a degree of blending between old and new binder and therefore to enhance mixture properties (see, e.g., Walter, 2002).
Material Variability
The gradation of RAP is quite different from the gradation of the original asphalt mixture, since it consists of agglomerates rather than individual particles, and the key difference is a much reduced fines content. This material variability needs to be considered when designing recycled asphalt mixtures (Sherwood, 2001).
Thanks for reading about “recycling of bituminous materials.”