Types of Carbon Steel
Carbon steels (or plain carbon steels) are ferrous metals. Percentage of carbon in them varies from about 0.05% to 2%. Accordingly they are classified as mild steel, medium carbon steel and high carbon steel. Mild steel is soft, medium carbon steel is tough, and high carbon steel is hard in comparison to each other. Following are the main types of carbon steel:
Types of Carbon Steel
- Wrought Iron
- Dead Mild Steel
- Low carbon Steel or Mild Steel
- Medium Carbon Steel
- High Carbon Steel
Wrought Iron
It is a mechanical mixture of pig iron and uniformly distributed silicate slag. It possesses the important properties of ductility, malleability and toughness. It is suitable for machine parts to be shaped by forging. It has also excellent welding properties. With the invention of steel, the use of wrought iron has decreased.
Applications: However, it is still used extensively for the following applications:
- chains and crane hooks,
- bolts subjected to shock loads,
- pipe and pipe fittings,
- culvert plates.
Its ultimate strength is about three quarters of that of structural steel, while the price is higher than that of mild steel.
Low-Carbon Steels
Of all the different types of steels, those produced in greatest quantities are of this type. These generally contain less than about 0.25 wt% C and are non-responding to heat treatments intended to form martensite. The strengthening is accomplished by cold work.
Microstructures consist of frerrite and pearlite constituents. As a consequence, these steels are relatively soft and weak. They, however have outstanding ductility and toughness. They are machineable, weldable and least expensive to produce.
Applications of Low-Carbon Steels
Following are the typical applications of low-carbon steels:
- automobile body components,
- structural shapes such as I-beams, channels and angle irons, etc.
- mild steel sheets that are used in pipelines, buildings, bridges etc.
- tin cans etc.
Some important mechanical properties of several plain low-carbon steels are as under:
- yield strength of about 275 MPa,
- tensile strengths between 415 and 550 MPa, and
- ductility of about 25%.
Medium-Carbon Steels
The medium-carbon steels have carbon concentrations between about 0.25 and 0.60 wt %. These alloys can be heat treated by austenitizing and quenching. They can be tempered to improve their mechanical properties. They are most often utilized in tempered condition, having microstructures of tempered martensite. The plain medium-carbon steels have low hardenabilities and can be heat treated only in the form of very thin sections by very rapid quenching rates.
Additions of chromium, nickel, and molybdenum improve the capacity of these alloys to be heat treated, giving rise to a variety of strength-ductility combinations. These heat-treated alloys are stronger than the low-carbon steels, but by sacrificing some ductility and toughness.
Applications of Medium-Carbon Steels
Following are the main applications of medium-carbon steels:
- railway wheels and tracks,
- crankshafts,
- high-strength structural components,
- gears,
- machine parts.
Such applications call for a combination of high strength, wear resistance, and toughness.
High-Carbon Steels
The high-carbon steels normally have carbon contents between 0.60 and 1.4 wt%. They are hardest, strongest and least ductile of all carbon steels. They are almost always used in a hardened and tempered condition.
They are especially wear resistant and capable of holding a sharp cutting edge. The tool and die steels are high-carbon alloys, usually containing chromium, vanadium, tungsten, and molybdenum. These alloying elements combine with carbon to form very hard and wear-resistant carbide compounds e.g., Cr23C6, V4C3 and WC.
Applications of High-Carbon Steels
These steels are utilized as follows:
- cutting tools and dies for forming and shaping materials,
- knives,
- hacksaw blades,
- high-strength wire, etc.
- razors,
- springs.
Ultrahigh-Carbon Steel (UHCS)
Ultrahigh-carbon steels are hypereutectoid steels having 1.0 to 2.1% carbon. Despite their high carbon content, they have remarkable mechanical properties. They are superplastic at intermediate and high temperatures.
At room temperatures, they have ultrahigh strengths with good ductility. They can be made exceptionally hard with high compression toughness by heat treatment.
- Laminated steel is an example of the bonding of low-and high-carbon cast strips.
- Cladded steels are made of stainless steel combined with low-carbon steels.
Effect of Carbon Content on Plain Carbon Steels
Percentage of carbon in steel influences its stress-strain profile. These profiles differ from one another in shape. In some cases, the slope of elastic curve is different and the yield point is higher or lower than one another. In other cases the ultimate stress (strength) points are higher or lower, and the fracture points show comparatively more or less strains. Different profiles characterize the change in properties as depicted in Figure 1(b).
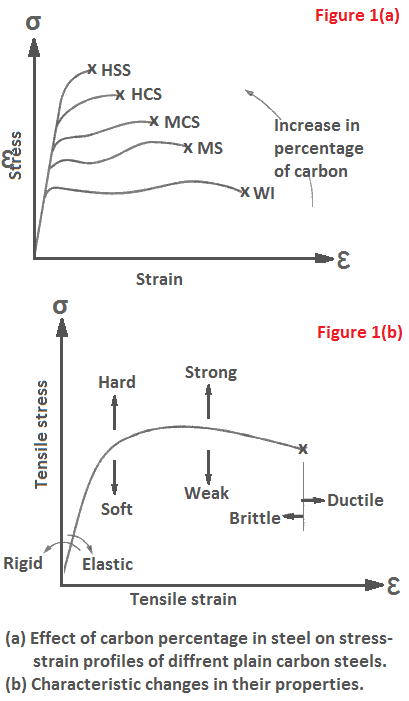
If the slope of elastic curve is more towards ordinate (σ-axis) than towards abscissa (e-axis), the material will be rigid. A harder material will keep its yield point higher. If the ultimate stress point shows a higher value, the material will be strong. A ductile material exhibits larger strain on fracture than a brittle material. Based on observations of Figure 1(b), we can conclude for Figure 1(a) that
- WI is most ductile and HSS is most brittle,
- HSS is hardest and WI is softest,
- TICS is strongest among plain carbon steels, and
- the slope of elastic curve is the same, hence stiffness is constant.
The depiction of Figure 1(b) holds good for all other materials.
Alloys
To meet the challenges of advance technology, the development of newer materials, particularly the alloys is very essential. The metals and their alloys have to work satisfactorily against wear, abrasion, toughness, high temperature hardness (red hardness), and electrical conduction etc. They have to be lightweight and economical too. Thus the need arises to develop heat resisting alloys, nuclear alloys, tool and die alloys, bearing alloys and others for specific uses.
Alloying elements are deliberately added in the base metal to achieve specific properties which are not found in the base metal. If one or more elements inhibit into the base metal accidently, they are then referred to as impurities. Chances of such accidents are more during smelting and refining processes.
The effects of various alloying elements are varying on different metals. Different purposes of adding alloying elements in steel are as follows.
- to form martensite without cracking of steel,
- to enhance hardenability,
- to increase red hardness (elevated temperature hardness),
- to distribute carbides during tempering,
- to provide wear and abrasion resistance,
- to impart toughness, and
- to increase ductility etc.
Based on the purpose served, the alloying elements are divided into two categories viz.
- austenite formers and,
- ferrite stabilizers or carbide formers.
The elements such as Ni, Co, Mn, C, N and Cu belong to the first category, while the second type of elements include Mo, W, Va, Ti, Cr, Nb, Sn and Si. Silicon is a graphitizing element that forms ferrite but does not form carbide. Effect of various alloying elements on Brinell hardness of ferritic iron is shown in Figure 2.
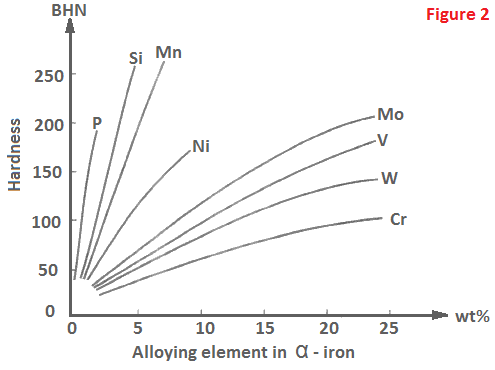
Alloy Steels
Plain carbon steels generally suffers from one or the other handicap in their mechanical properties for specific uses. But they show remarkable improvement when alloyed with one or more elements.
This is why the alloys have more industrial applications than the pure metals. Various elements are used to alloy with steel. Each of them has a particular effect on the properties of steel. Different alloying elements and their notable effects are as under:
Tungsten | W | Imparts red hardness |
Vanadium | V | Induces fine grain distribution |
Chromium | Cr | Improves resistant to corrosion and oxidation |
Molybdenum | Mo | Increases hardenability |
Manganese | Mn | Imparts wear resistance |
Titanium | Ti | Increases abrasion resistance |
Nickel | Ni | Improves tensile strength and toughness |
Phosphorus | P | Enhances machinability |
Stainless Steels
The stainless steels are highly resistant to corrosion (rusting) in a variety of environments, especially the ambient atmosphere. Their predominant alloying element is chromium in which a concentration of at least 11 wt% Cr is required. Corrosion resistance may also be enhanced by adding nickel and molybdenum.
Stainless steels are divided into three different classes on the basis of the phase constituent of the microstructure. These are:
- Martensitic stainless steel
- Ferritic stainless steel
- Austenitic stainless steel
A wide range of mechanical properties combined with excellent resistance to corrosion make stainless steels very versatile in their applicability. Main features of different classes of stainless steels are as follows.
- Martensitic stainless steels are capable of being heat treated in such a way that the martensite is the prime microconstituent.
- Additions of alloying elements in significant concentration produce dramatic alterations in the iron-iron carbide phase diagram. For austenitic stainless steels, the austenite (or y) phase is extended to room temperature.
- Ferritic stainless steels are composed of the α ferrite (BCC) phase.
- Austenitic and ferritic stainless steels are hardened and strengthened by cold work because they are not heat treatable.
- The austenitic stainless steels are the most corrosion resistant because of the high chromium contents and addition of the nickel. They are produced in the largest quantities.
- Both martensitic and ferritic stainless steels are magnetic, the austenitic stainless steel are not.
Applications: Some stainless steels are frequently used at elevated temperatures and in severe environments because they resist oxidation and maintain their mechanical integrity under such conditions. Following are the typical applications of such stainless steels.
- High temperature steam boilers.
- Heat treating furnace.
- Aircrafts, missiles, and nuclear power generating units.
- The upper temperature limit in oxidizing atmospheres is about 1000°C. Equipment employing these steels includes gas turbines.
There is an ultrahigh-strength stainless steel also which is unusually strong and corrosion resistant. Strengthening is accomplished by precipitation-hardening heat treatment.
Marageing Steel
These are high-strength high alloy steels containing high nickel content. The term marageing comes from age-hardening (or ageing) of martensite i.e. mar + ageing. Such steels are very costly, therefore, their uses is limited to sophisticated technology such as rocketry.
It is available in different grades. Their approximate compositions are Ni 17 to 18%, Co 8 to 12%, Mo 3 to 5%, Ti 0.2 to 1.8%, Al 0.05 to 0.15%, Fe rest percentage. Mechanical properties of marageing steels are as under:
- Tensile strength = 1500 to 2500 MPa
- Value at 0.2% proof stress = 1900 Mpa
- Elongation = 5 to 12%
They are used for motor casing of booster rockets.
Nickel-Molybdenum Steel Alloy
There are several nickel-molybdenum alloys which are very much resistant to corrosion. These alloys are called Hatelloys. They are sub-classified as Hastelloy A, C, and D according to their composition.
Hastelloy A: It is nickel-molybdenum-iron alloy. It has high strength and ductility. Its strength does not decrease even at high temperature and it can withstand a load of 110 kg/cm2 at 900°C with a creep of 1% per year. Also
- It can be easily forged and rolled into sheet.
- It can be machined, and can form good castings.
- It can be welded by oxy-acetylene or electric arc method.
- It can resist the attack of even concentrated HCl at boiling point.
- It is resistant to concentrated sulfuric acid up to 70°C. It resists the attack of acetic and formic acids also but not of nitric acid.
- Alkalies do not attack it. Salt solutions also have no effect on it.
Hastelloy C: It is nickel-molybdenum-chromium-iron alloy. Its malleability is less than that of Hastelloy A. It cannot be worked hot or cold.
- It is good for castings but cannot be machined at high speed.
- It is resistant to strong oxidizing agents such as nitric acid, free chlorine and acid solutions of salts such as cupric and ferric. In this respect, it is an improvement over Hastelloy A.
Hastelloy D: It is cast alloy consisting of nickel, silicon, copper and aluminum. It is strong is tough, and has a high transverse strength.
- It is good for casting, but cannot be hot or cold worked.
- Its machinability is poor.
- It can be welded with oxy-acetylene or electric arc method. We can make the operation easy with an addition of a flux.
- It is resistant to all acids except nitric acid.
Heat Resisting Alloys
Quite often we need temperature measurement of furnaces and ovens in different industries for a proper process control. We invariably need use of heat resisting alloys is such applications. Besides using common alloys, nickel based superalloys are widely used for this purpose.
Characteristics: Heat-resisting steels resist oxidation at high temperatures and in some cases, attack by sulphurous gases. For this reason they contain as much as 30% chromium together with small amounts of Si. The general tendency for chromium to induce grain growth with its brittleness, it offset by adding nickel.
These steels are supposed to be reasonably strong at high temperatures, therefore they are stiffened by adding small amounts of carbon, tungsten, molybdenum, titanium and aluminum. This causes formation of carbides or intermetallic compounds.
Metallurgical principles involved in the heat-resisting steels also apply to the `Nimonic’ series of alloys. These are not steels but contain basically 75% Ni +20%Cr, stiffened with small amounts of carbon, titanium, aluminum, cobalt, molybdenum or niobium.
Superalloys
The superalloys have superlative combinations of properties. Most of these are used in aircraft turbine components, which withstand exposure to severely oxidizing environments and high temperatures for reasonable period of time.
Mechanical integrity under these conditions is critical. In this regard, the density is an important consideration because the centrifugal stresses are diminished in rotating members when density is reduced.
These materials are classified on the basis of dominant metal in the alloy. It may be cobalt, nickel, or iron. Other alloying elements include the refractory metals such as Nb, Mo, W, Ta, chromium and titanium. In addition to turbine applications, these alloys are also utilized in nuclear reactors and petrochemical equipment.
Types of superalloys: Superalloys are a group of high performance alloys designed to meet very demanding requirements for strength and resistance to surface degradation at high service temperatures. These may be iron-based, nickel-based, and cobalt-based as given below.
Iron based superalloys: The composition of such superalloys are iron 30 – 50% + nickel 20 – 30% + cobalt 20% + chromium 15 – 21% + other alloying elements such as titanium, molybdenum etc. Incoloy having 46% Fe, 32% Ni, 21% Cr, <1% Ti, < 1% other elements is an example.
Nickel based superalloys: The composition of such superalloys is: nickel 40 – 76% nickel + chromium 16 – 21% + cobalt 8 – 11% + other alloying elements such as aluminum, titanium, molybdenum, niobium and iron. Nimonic having 3% Fe, 76% Ni, 20% Cr, < 1% Ti, < 1% other other elements is an example.
Cobalt based superalloys: The composition of such superalloys is: cobalt 39 – 53 % + chromium 20 – 30% + nickel 3 – 22% + other alloying elements such as molybdenum, tungsten, and iron.
Following are the some main applications of superalloys:
- gas turbines,
- jet and rocket engines,
- steam turbines,
- aircraft turbine components,
- nuclear power plants,
- petrochemical equipment.
Cryogenic Steel
Nickel based cryogenic steel have been developed for use in cryogenic industries. Cryogenic processes involved in these industries are carried out at temperatures below – 157.5oC. The storage and transport of liquefied gases for industrial and domestic purposes are done at much lower temperature.
For example, oxygen, nitrogen and ammonia are liquefied at –183oC,
–196oC and –190oC respectively. Also, the vital parts of human body are stored at much lower temperatures. To serve these purposes, various nickel based cryogenic steels are used. Their compositions and service temperatures are as under:
Percentage of nickel | 3.5 | 5.0 | 9.0 |
Service temperature (oC) | – 100 | –120 | –190 |
High-Strength Low-Alloy (HSLA) Steel
HSLA steel is a product of recent technology aimed at producing strong, lightweight steel at a competitive price with that of carbon steels. It has a higher strength of 415 kPa versus 275 kPa for carbon steel. Consequently, the overall cost may be cheaper for the HSLA and significant weight savings are realized. The transportation industry, especially the automotive section, employs HSLA steel in numerous structural applications.
Some HSLA steels, called microalloyed steel, contain micro amounts of elements such as nitrogen, titanium, aluminum, or niobium that form carbides or nitrides in the austenite. It thus, prevents the growth of the austenite grains. These steels gain their strength without the need for heat treating through the ability to control their grain growth. Weighing less than regular alloy steels but with increased yield strengths (290-480 MPa), these economical steels are ideal for the manufacturing of bridges, off-highway vehicles, ships, machinery etc. Possessing good weldability, they are produced for sheet, plate, pipe, and forging applications.
Other Alloy Steels
The list of varieties of alloy steels is too lengthy. But we shall restrict our studies to some more important alloy steels, given as follows.
Free cutting steel: A free-cutting steel is one in which an element like lead or sulfur is deliberately added to promote rapid machining. When sulfur is added to steel, it forms a brittle constituent with manganese, which is known as manganese sulfide (MnS).
The MnS being brittle allows the chip cracks to propagate and to break the chips into easily handleable lengths. Contrary to this, the lead (Pb) does not chemically combine with other elements. It gets distributed throughout the mass as minute droplets. Thus the chip cracks are propagated easily and the chips come out in easily handled lengths.
Wear resisting steels: These contain carbon from 1 to 1.2%. Addition of 12.5% manganese makes austenite to be retained after heating and quenching. This alloy is known as `Hadfields’ austenitic steel, which responds to work hardening and becomes harder as a result of rough treatment. Accordingly, it is used for track work, dredging equipment and crushing machinery.
Steels with 1.4% chromium and 0.45% manganese can be oil-quenched and are very hard. They are used for making roller and ball races.
© https://civilengineeringcourses.com/ types of carbon steel.