Properties of Polymers
Polymers are materials consisting of long-chain molecules formed primarily by carbon-to-carbon bonds. Examples include all materials commonly referred to as plastics, most familiar natural and synthetic fibers, rubbers, and cellulose and lignin in wood. Polymers that are produced or modified by man for use as engineering materials can be classified into three groups: thermoplastics, thermosetting plastics, and elastomers.
When heated, a thermoplastic softens and usually melts; then, if cooled, it returns to its original solid condition. The process can be repeated a number of times. However, a thermosetting plastic changes chemically during processing, which is often done at elevated temperature. It will not melt upon reheating, but will instead decompose, as by charring or burning.
Elastomers are distinguished from plastics by being capable of rubbery behavior. In particular, they can be deformed by large amounts, say 100% to 200% strain or more, with most of this deformation being recovered after removal of the stress. Examples of polymers in each of these groups are listed, along with typical uses, in Table 1.
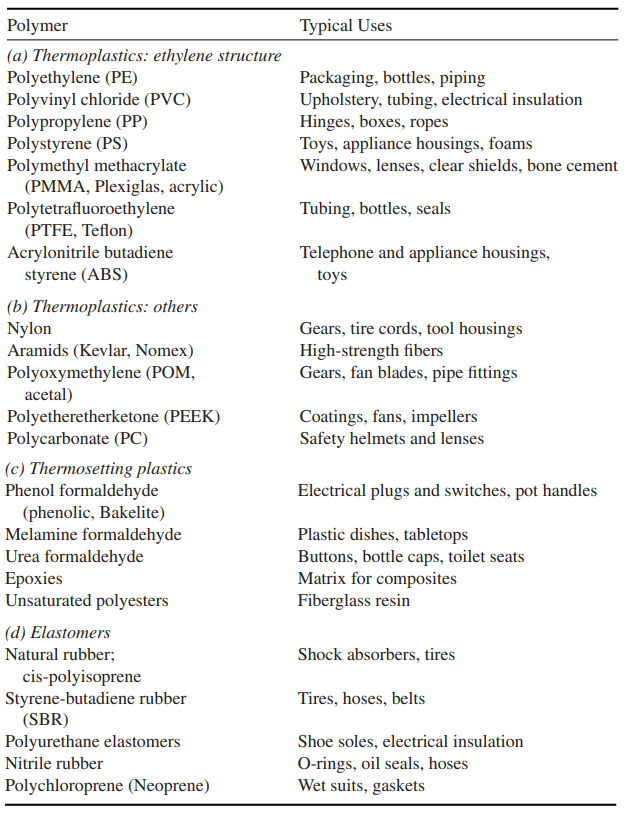
After chemical synthesis based primarily on petroleum products, polymers are made into useful shapes by various molding and extrusion processes, two of which are illustrated in Fig. 1. For thermosetting plastics and elastomers that behave in a similar manner, the final stage of chemical reaction is often accomplished by the application of temperature and/or pressure, and this must occur while the material is being molded into its final shape.
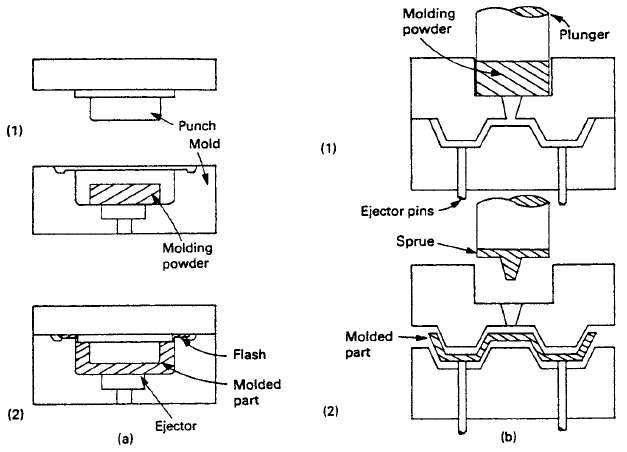
Properties of Polymers
Polymers are named according to the conventions of organic chemistry. These sometimes lengthy names are often abbreviated by acronyms, such as PMMA for polymethyl methacrylate. In addition, various trade names and popular names, such as Plexiglas, Teflon, and nylon, are often used in addition to, or in place of, the chemical names.
An important characteristic of polymers is their light weight. Most have a mass density similar to that of water, around ρ = 1 g/cm3, and few exceed ρ = 2 g/cm3. Hence, polymers are typically half as heavy as aluminum (ρ = 2.7 g/cm3) and much lighter than steel (ρ ≈ 7.9 g/cm3). Most polymers in unmodified form are relatively weak, with ultimate tensile strengths typically in the range 10 to 200 MPa.
In the discussion that follows, we first consider the basic molecular structure of typical polymers in each group. This provides the background for later discussion of how the details of molecular structure affect the mechanical properties.
Molecular Structure of Thermoplastics
Many thermoplastics have a molecular structure related to that of the hydrocarbon gas ethylene, C2H4. In particular, the repeating unit in the chain molecule is similar to an ethylene molecule, except that the carbon-to-carbon bond is rearranged . The molecular structures of some of the simpler polymers of this type are illustrated by giving their repeating unit structures in Fig. 2.
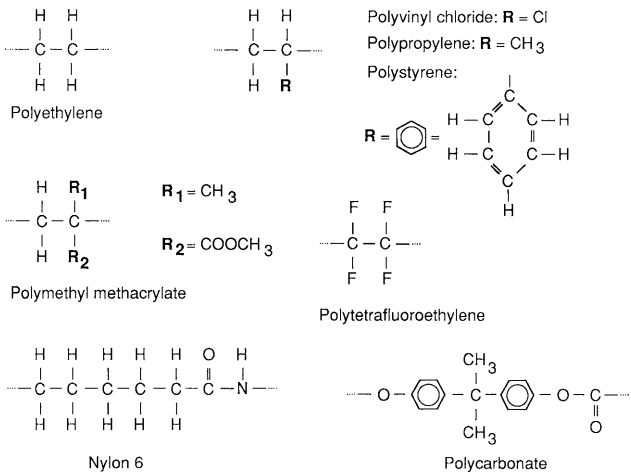
Polyethylene (PE) is the simplest case, in that the only modification to the ethylene molecule is the rearranged carbon-to-carbon bond. In polyvinyl chloride (PVC), one of the hydrogen atoms is replaced by a chlorine atom, whereas polypropylene (PP) has a similar substitution of a methyl (CH3) group. Polystyrene (PS) has a substitution of an entire benzene ring, and PMMA is based on two substitutions, as shown.
Polytetrafluoroethylene (PTFE), also known as Teflon, has four fluorine substitutions. Ethylene-based thermoplastics are by far the most widely used plastics, with PE, PVC, PP, and PS accounting for more than half the weight of plastics usage.
However, other classes of thermoplastics that are used in smaller quantities are more suitable for engineering applications where high strength is needed. The engineering plastics include the nylons, the aramids such as Kevlar, polyoxymethylene (POM), polyethylene terephthalate (PET), polyphenylene oxide (PPO), and polycarbonate (PC). Their molecular structures are generally more complex than those of the ethylene-based thermoplastics. The repeating unit structures of two of these, nylon 6 and polycarbonate, are shown as examples in Fig. 2.
Other nylons, such as nylon 66 and nylon 12, have more complex structures than nylon 6. Kevlar belongs to the polyamide group, along with the nylons, and has a related structure involving benzene rings, so that it is classed as an aromatic polyamide, that is, an aramid.
Crystalline Versus Amorphous Thermoplastics
Some thermoplastics are composed partially or mostly of material where the polymer chains are arranged into an orderly crystalline structure. Examples of such crystalline polymers include PE, PP, PTFE, nylon, Kevlar, POM, and PEEK. A photograph of crystal structure in polyethylene is shown as Fig. 3.
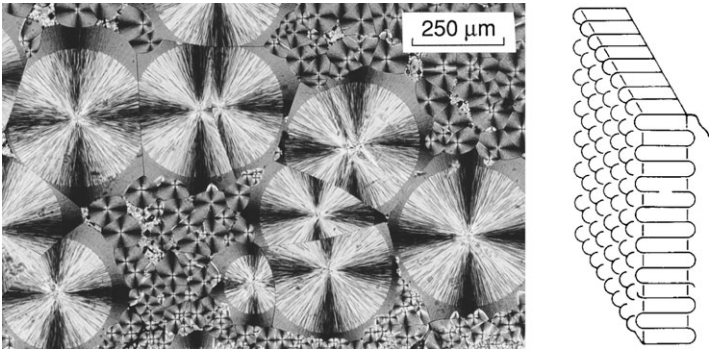
are seen edge-on in the photo, being arranged in a radiating pattern to form the
prominent crystalline features called spherulites.
If the chain molecules are instead arranged in a random manner, the polymer is said to be amorphous. Examples of amorphous polymers include PVC, PMMA, and PC. Polystyrene (PS) is amorphous in its atactic form where the benzene ring substitution is randomly located within each repeating unit of the molecule, but is crystalline in the isotactic form where the substitution occurs at the same location in each repeating unit.
This same situation occurs for other polymers as well, due to the regular structure of the isotactic form promoting crystallinity. If the side groups alternate their positions in a regular manner, the polymer is said to be syndiotactic, with a crystalline structure being likely in this case also.
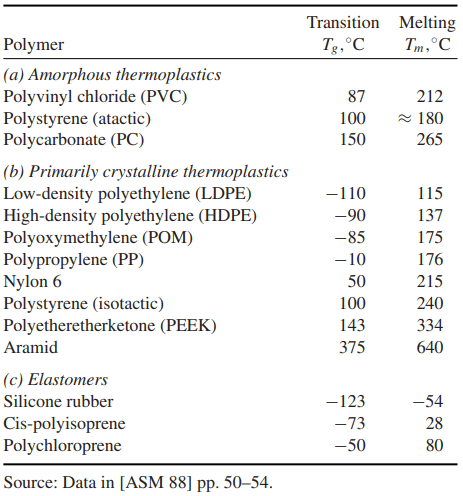
Amorphous polymers are generally used around and below their respective glass transition temperatures Tg, some values of which are listed in Table 2. Above Tg, the elastic modulus decreases rapidly, and time-dependent deformation (creep) effects become pronounced, limiting the usefulness of these materials in load-resisting applications.
Their behavior below Tg tends to be glassy and brittle, with the elastic modulus being on the order of E = 3 GPa. Amorphous polymers composed of single-strand molecules are said to be linear polymers. Another possibility is that there is some degree of branching, as shown in Fig. 4.
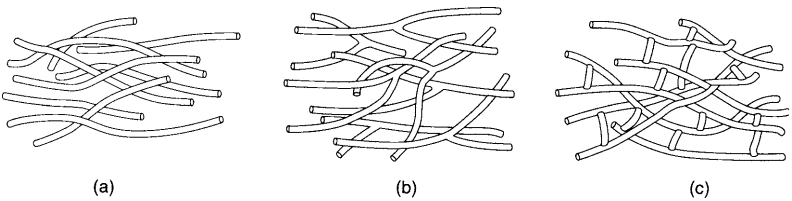
Crystalline polymers tend to be less brittle than amorphous polymers, and the stiffness and strength do not drop as dramatically beyond Tg. For example, such differences occur between the amorphous and crystalline forms of PS, as illustrated in Fig. 3.15.
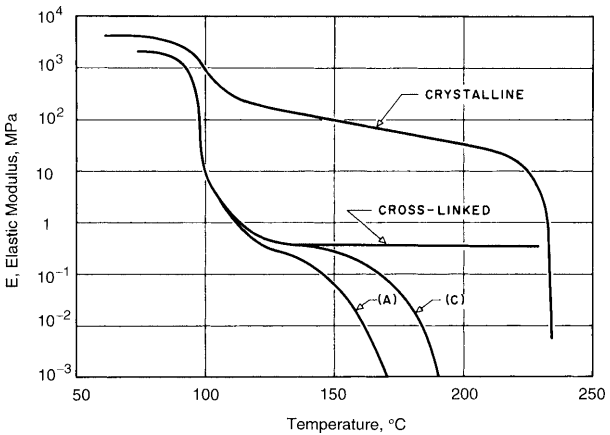
As a result of this behavior, many crystalline polymers can be used above their Tg values. Crystalline polymers tend to be opaque to light, whereas amorphous polymers are transparent.
Thermosetting Plastics
The molecular structure of a thermosetting plastic consists of a three-dimensional network. Such a network may be formed by frequent strong covalent bonds between chains, called cross-links, as illustrated in Fig. 4(c). In some cases, most repeating units have three carbon–carbon bonds to other units, so that the cross-linking is maximized. This is the case for phenol formaldehyde (phenolic), the structure of which is shown in Fig. 3.16. The common plastic Bakelite is a phenolic. Some other common thermosetting polymers are the epoxy adhesives and polyester resins used for fiberglass.
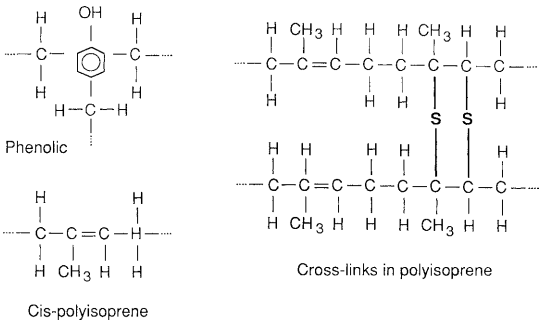
and of a synthetic similar to natural rubber, cis-polyisoprene. In the phenolics, carbon–carbon bonds form cross-links, whereas in polyisoprene cross-links are formed by sulfur atoms.
The cross-linking (thermosetting) chemical reaction occurs during the final stage of processing, which is typically compression molding at elevated temperature. Following this reaction, the resulting solid will neither soften nor melt upon heating, but will usually decompose or burn instead. The network structure results in a rigid and strong, but brittle, solid.
Recall that thermal expansion and the resulting increased free volume produces the glass transition temperature (Tg) effect in thermoplastics, above which deformation may occur by relative sliding between chain molecules.
This situation contrasts with that for a thermosetting plastic where relative motion between the molecules is prevented by strong and temperature-resistant covalent bonds. As a result, there is no distinct Tg effect in highly cross-linked thermosetting plastics.
Elastomers
Elastomers are typified by natural rubber, but also include a variety of synthetic polymers with similar mechanical behavior. Some elastomers, such as the polyurethane elastomers, behave in a thermoplastic manner, but others are thermosetting materials. For example, polyisoprene is a synthetic rubber with the same basic structure as natural rubber, but lacking various impurities found in natural rubber.
This structure is shown in Fig. 6. Adding sulfur and subjecting the rubber to pressure and a temperature around 160◦C causes sulfur cross-links to form, as shown. A greater degree of cross-linking results in a harder rubber. This particular thermosetting process is called vulcanization
Although cross-linking results in the rigid network structure of thermosetting plastics, typical elastomers behave in a very different manner because the cross-links occur much less frequently along the chains, specifically at intervals on the order of hundreds of carbon atoms. Also, the cross-links and the main chains themselves are flexible in elastomers, rather than stiff as in the thermosetting plastics.
This flexibility exists because the geometry at the carbon-to-carbon double bond causes a bend in the chain, which has a cumulative effect over long lengths of chain, such that the chain is coiled between cross-link points. Upon loading, these coils unwind between the crosslink attachment points, and after removal of the stress, the coils recover, resulting in the macroscopic effect of recovery of most of the deformation. Typical deformation response is shown in Fig. 7.
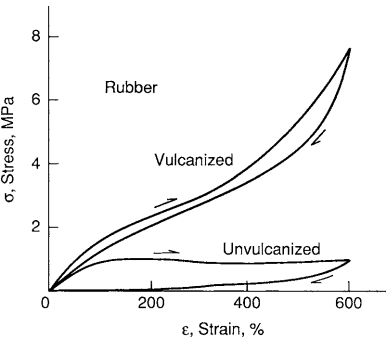
The initial elastic modulus is very low, as it is associated only with uncoiling the chains, resulting in a value on the order of E = 1 MPa. Some stiffening occurs as the chains straighten. This low value of E contrasts with that for a glassy polymer below its Tg, where elastic deformation is associated with stretching the combination of covalent and secondary chemical bonds involved, resulting in a value of E on the order of 1000 times higher.
Strengthening Effects
The molecular structures of polymers are affected by the details of their chemical synthesis, such as the pressure, temperature, reaction time, presence and amount of catalysts, and cooling rate. These are often varied to produce a wide range of properties for a given polymer. Any molecular structure that tends to retard relative sliding between the chainlike molecules increases the stiffness and strength. Longer chain molecules—that is, those with a greater molecular weight—have this effect, as longer chains are more prone to becoming entangled with one another.
Stiffness and strength are similarly increased by more branching in an amorphous polymer, by greater crystallinity, and by causing some cross-linking to occur in normally thermoplastic polymers. All of these effects are most pronounced above Tg, where relative sliding between chain molecules is possible.
For example, one variant of polyethylene, called low-density polyethylene (LDPE), has a significant degree of chain branching. These irregular branches interfere with the formation of an orderly crystalline structure, so that the degree of crystallinity is limited to about 65%.
In contrast, the high-density variant HDPE has less branching, and the degree of crystallinity can reach 90%. As a result of the structural differences, LDPE is quite flexible, whereas HDPE is stronger and stiffer
An extreme variation in the properties of rubber is possible by varying the amount of vulcanization, resulting in different degrees of cross-linking. The effect on the elastic modulus (stiffness) of the synthetic rubber polyisoprene is shown in Fig. 8.
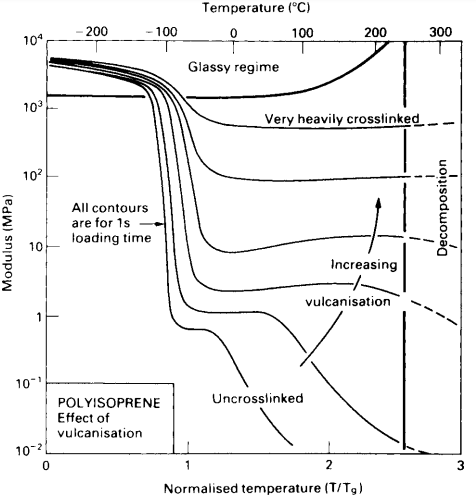
Unvulcanized rubber is soft and flows in a viscous manner. Cross-linking by sulfur at about 5% of the possible sites yields a rubber that is useful in a variety of applications, such as automobile tires. A high degree of crosslinking yields a hard and tough material called ebonite that is capable of only limited deformation.
Combining and Modifying Polymers
Polymers are seldom used in pure form, often being combined with one another or with other substances in various ways. Alloying, also called blending, involves melting two or more polymers together so that the resulting material contains a mixture of two or more chain types.
This mixture may be fairly uniform, or the components may separate themselves into a multiphase structure. For example, PVC and PMMA are blended to make a tough plastic with good flame and chemical resistance
Copolymerization is another means of combining two polymers, in which the ingredients and other details of the chemical synthesis are chosen so that the individual chains are composed of two types of repeating units.
For example, styrene–butadiene rubber is a copolymer of three parts butadiene and one part styrene, both of which occur in most individual chain molecules. ABS plastic is a combination of three polymers, called a terpolymer. In particular, the acrylonitrile–styrene copolymer chain has side branches of butadiene polymer
Among the nonpolymer substances added to modify the properties of polymers are plasticizers. These generally have the objective of increasing toughness and flexibility, while often decreasing strength in the process. Plasticizers are usually high-boiling-point organic liquids, the molecules of which distribute themselves through the polymer structure.
The plasticizer molecules tend to separate the polymer chains and allow easier relative motion between them—that is, easier deformation. For example, plasticizers are added to PVC to make flexible vinyl, which is used as imitation leather
Polymers are often modified or filled by adding other materials in the form of particles of fibers. For example, carbon black, which is similar to soot, is usually added to rubber, increasing its stiffness and strength, in addition to the effects of vulcanization. Also, rubber particles are added to polystyrene to reduce its brittleness, with the resulting material being called high-impact polystyrene (HIPS). The microstructure of a HIPS material is shown in Fig. 3.19.
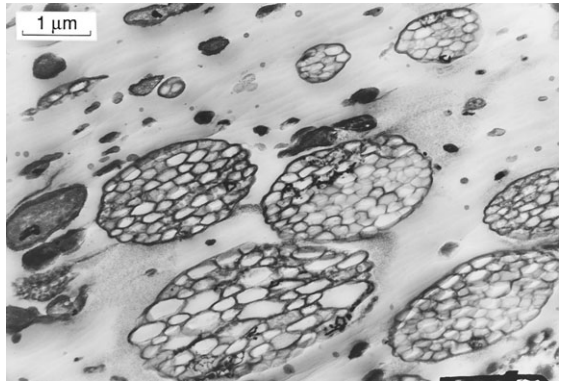
If the added substance has the specific purpose of increasing strength, it is called a reinforcement. For example, chopped glass fibers are added as reinforcement to various thermoplastics to increase strength and stiffness.
Reinforcement may also take the form of long fibers or woven cloth made of high-strength fibers, such as glass, carbon in the form of graphite, or Kevlar. These are often used in a matrix of a thermosetting plastic. For example, fiberglass contains glass fibers in the form of mats or woven cloth, and these are embedded in a matrix of unsaturated polyester. Such a combination is a composite material.
Thanks for reading about “properties of polymers.”