Properties of Mortar
Mortar has to cope with a wide range of sometimes conflicting requirements. To obtain optimum performance the composition must be tailored to the application. The broad principles are as follows:
- Mortars with a high content of hydraulic cements are stronger, denser, more impervious and more durable, bond better to units under normal circumstances and harden rapidly at normal temperatures. They also lead to a high drying shrinkage and rigidity of the masonry. They are likely to cause shrinkage cracks if used with shrinkable low strength units particularly for long lightly loaded walls such as parapets and spandrels.
- Mortars with decreased or no content of hydraulic cements are weaker and more ductile and thus more tolerant of movement. They are matched better to low-strength units but at the cost of a reduction in strength, durability and bond. There is a corresponding reduction in shrinkage and hardening rate.
- Mortars made with sharp, well-graded sands can have very high compressive strength, low permeability and generally good bond but poor workability. Fine loamy sands give high workability but generally with reduced compressive strength and sometimes reduced bond.
- Lime confers plasticity and, particularly for the wet stored mixes, water retentivity (the ability of the mortar to retain its water in contact with highly absorbent bricks), which facilitates the laying process and makes sure that the cement can hydrate. Lime mortars perform poorly if subjected to freezing while in the green (unhardened) state but, when hardened, are very durable. Lime is white and thus tends to lighten the colour of the mortar. In some circumstances it can be leached out and may cause staining.
- Air entrainment improves the frost resistance of green mortar and allows lower water:cement ratios to be used, but such plasticised mixes may be less durable and water-retentive than equivalent lime mixes. Air-entrained mixes also need careful manufacture and control of use since over-mixing gives very high air contents, and retempering (adding more water and reworking the mix) can lead to very poor performance owing to the high porosity of the set dry mortar.
- Pigments weaken mortar and their content should never exceed the doses.
- Polymer latex additives can markedly improve some properties, but they are expensive.
- Retarders are widely used in the manufacture of ready-mixed mortars, delivered to site in the same way as ready-mixed concrete. The retarder is dosed to give a ‘pot life’ of between 1 and 3 days. Care is needed in the use of retarded mortars, especially in hot dry weather, because if they dry out too rapidly the curing process does not take place and the mortar only hardens when finally wetted.
- Mortar has a relatively high thermal conductivity and thus causes heat loss in walls of insulating units. Insulating mortars, which use a low-density replacement for the coarse sand particles, can give improved performance. Another option is to use 1–5 mm thick joints of high-bond ‘thin-bed mortars’ with units with close tolerances on their size (see BRE Digest 432 (1998)).
Properties of Freshly-Mixed (Unset) Mortar
Test methods for fresh mortar are given in the BS EN1015 series of standards (1998–1999) and a few in BS 4551 (1980), RILEM (1978) and ISO (1991). A key property of unset mortar is the workability, i.e. how easy it is to handle and place on to the masonry. This is covered either by the flow test, measured on a standard 254 mm diameter (ASTM) flow table covered by BS EN1015-3 (1999) or by consistence, measured by the plunger penetration test in EN1015-4 (1999).
Other useful measurements are: the pot life and the setting time, i.e. how long it may be used for after mixing (see EN1015-9 (1999)); the water retentivity, i.e. how good it is at retaining water against the suction of the units measured in accordance with BS 4551 (1980); and the hardening rate.
Associated parameters are the cement content, water content (often expressed as the water:cement ratio, w/c) and the air content, measured by weighing a known volume (0.5 litres) of mortar and then calculating, using the relative densities and proportions of the constituents, from equation 1 (see BS EN1015-7, 1999):
A = 100(1 − kρ) …….(1)
where A is the air content, ρ is the relative density of the mortar and K is derived from:
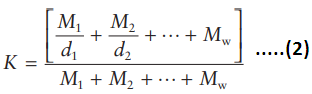
where M1, M2,…, etc. are the relative masses of the constituents of the mortar of relative densities (specific gravities) d1, d2, etc., and Mw is the relative mass of water. The sum of all the values of M1, M2,… and Mw will be equal to 1.
For precise measurements it is necessary to measure the relative densities of all the individual constituents by use of the density bottle method. If this cannot be done the following default values are suggested: Portland cement, 3.12; masonry cement, 3.05; silica sand, 2.65; white hydrated building lime, 2.26; and grey hydrated lime, 2.45. Alternatively the pressure method can be used.
The water content can be determined independently on fresh mortar by rapid oven drying of a weighed quantity. A simple site test to independently measure the cement content of fresh and unhardened mortars has been described by Southern (1989) and de Vekey (2001).
A quantity of mortar is weighed and dissolved in a pre-diluted and measured volume of acid held in an insulated container. The cement content can be calculated from the temperature rise measured with an electronic thermometer.
Properties of Hardened Mortar
The important properties of hardened mortar are its density, permeability, compressive plus flexural strength and bond strength to units; methods of measuring these are described in BS EN1015-6 (1999), BS EN1015-19 (1999), BS EN1015-11 (1999) and BS EN1052-5 (2005), respectively.
The compressive strength is measured by a cube-crushing test and the flexural strength is measured by the three point bend (or modulus of rupture) test. Other useful indicators of performance are the drying shrinkage and Young’s modulus, which may be measured by tests given in BS 4551 (1980), RILEM (1978) or ISO (1991). Durability is influenced by the combination of other properties and may be determined using the methods proposed by Harrison (1981, 1986), Harrison and Bowler (1990) and Bowler et al. (1995), now standardised by RILEM (1998).
The bond strength to typical units can be measured by the parallel wallette test. In this test a small wall is built and tested in the vertical attitude by a four-point bend test using articulated loading arms and supports, to prevent the application of any twisting moments, and resilient bolsters to prevent uneven loading.
The alternative bond wrench, which has been included in some codes and standards (such as ASTM C1072-86 (1986) and Standards Association of Australia (1988)), is now the basis of BS EN1052-5 (2005). It is a simpler way to measure bond strength than the wallette test although it may give slightly higher values.
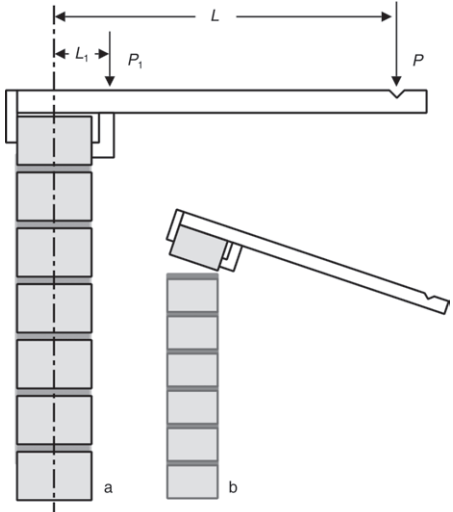
This device measures the moment required to detach a single unit from the top of a wall or stack-bonded prism using a lever clamped to the unit (Fig. 1). The load may be applied in a variety of ways, most simply by filling a container with lead shot. An electronically gauged version is described in BRE Digest 360 (1991) where the load is applied via a load cell transducer. Its main advantage is that it can be used both on site for quality control and diagnosis of problems and failures and as a laboratory tool.
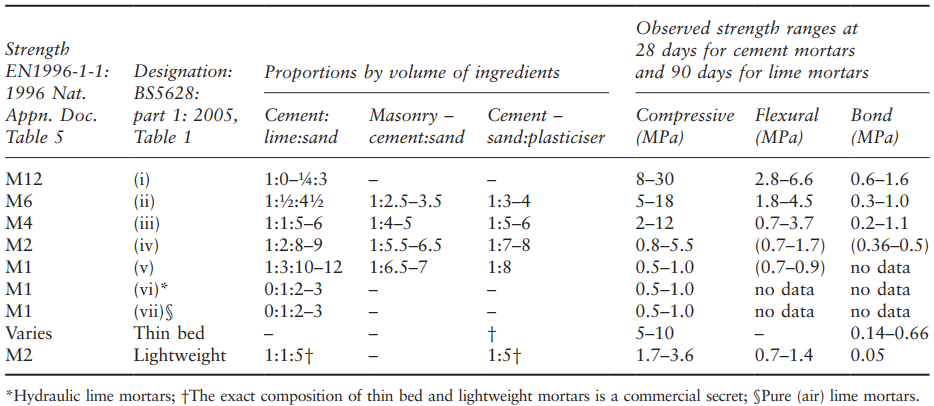
Table 1 gives the common formulations of mortars in contemporary use and also lime mortars for restoration work. The table gives some ranges for the performance of mortars in terms of the range of their compressive, flexural and bond strengths.
A ‘designation’ is a term used for a group of prescribed mortars giving approximately similar performance. The table also includes the equivalent performance measures used by the Eurocode and associated standards. This is based on compressive strength and expressed as MXX (where XX is the target value).
It is clear from the table that a very wide range of strengths is possible for any nominal mix ratio and that parameters other than just the binder type and content influence the strength, including the water:cement ratio, sand grading and air content. A further factor, which only affects the properties of the mortar in the bed (and not, of course, mortar specimens cast in impervious moulds), is the amount of dewatering and compaction by the units.
Where dewatering occurs it generally increases the intrinsic strength and density of the mortar but may reduce the bond by also causing shrinkage and local microcracking. Other key parameters are porosity (indicative of permeability), Young’s modulus and drying shrinkage.
Density (ρ) is obtained by dividing the weight of a prism or cube by its volume, which may be obtained by measuring all the dimensions; alternatively the density can be obtained by weighing the prism/cube submerged in water and then calculating:
ρ = m/bdL or ρ = m/(m − ms) …….(3)
where m is weight in air, b is the width, d is the depth and L is the length of the prism/cube, and ms is its weight when submerged.
The density will vary with moisture content and W is measured as saturated or oven dry. Typical densities for mortars are usually in the range 1500–2000 kg/m3. The water porosity is obtained by measuring the water absorption by evacuating the weighed dry specimen then immersing it in water at atmospheric pressure and weighing. The gain in weight of water can be converted to volume and then divided by the volume of the specimen to give the percentage porosity.
The Young’s modulus may be derived from the flexural strength test provided deflection is measured. Drying shrinkage is measured by attaching precision reference points to the ends of a prism, saturating the prism with water and measuring the length with a micrometer screw gauge or other precision length-measuring device.
After a drying regime the length is again measured and the change is expressed as a percentage of the overall length. Various drying regimes have been used (BRE Digest 35 (1963), RILEM (1975) and CEN (2002)).
Thin-bed and lightweight mortars Thin-bed mortars (see BRE Digest 432, 1998; Fudge and Barnard, 1998; and Phillipson et al., 1998) are proprietary formulas but normally contain some fine sand and cement plus bond-improving additives. They are normally supplied as a dry premix that just needs thorough mixing with water before use.
The application technique is similar to that used for bedding tiles by use of serrated spreaders to produce thin ribbed layers of the order of 2–5 mm thick. Accurate levelling is crucial for good quality work. Lightweight mortars (see Stupert et al., 1998) are thermally more efficient replacements for normal mortars and contain cement, optionally lime and low-density fine aggregates such as pumice, pfa and perlite.
Thanks for reading about “properties of mortar”.