Polymerization | Processing of Plastics
Materials derived from carbon are termed as organic materials. Range of organic materials is in thousands owing to vast variety of hydrocarbons and their derivatives. Organic materials may be natural or synthetic.
Petroleum rubber wood coal biological fibers food etc. cotton flax are examples of natural organic materials. And oil solvent lubricant adhesive dye synthetic rubber plastics explosive etc. are examples of synthetic organic materials.
Organic materials are covalent (polar) bonded. Polymers such as plastics, synthetic rubber and wood are common organic materials of important engineering applications.
Meaning of Monomers and Polymers
A monomer is a small molecule, which on polymerization converts into a large molecule (macromolecule) called polymer. Polymerization is the process of linking of monomers under suitable conditions of temperature and pressure.
Polymers arc composed of large number of monomers. `Poly’ means ‘many’ and `mer’ means unit. Thus polymers are large number of repeating monomers. Their molecular configuration may be that of a long chain or network.
Polymers are generally non-crystalline solids. Their mechanical properties are highly sensitive to molecular configuration, degree of polymerization and cross-linking.
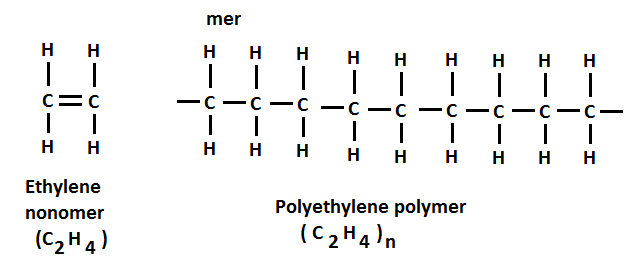
Linking of an ethylene monomer (C2H4) to form polyethylene (C2H4)n is shown in Figure 1. Two single bonds (C – C) in polymer are formed from each double bond (C=C) in the monomer.
Polymers are mostly made from carbon compounds but can also be made from inorganic silicates and silicons. They are also found in natural form. Protein, cellulose and starch etc. are examples of natural polymers. And polythene, polystyrene and nylon etc. are examples of synthetic polymers.
Degree of Polymerization
The size of macromolecule depends on the number of repeating monomers constituting it. It is designated by Degree of Polymerization (DOP), and is defined as
DOP = Molecular weight of polymer/ Molecular weight of monomer = Mp/Mm
A lower value of DOP forms light oil, and a higher value results into a solid plastics. Generally a molecule contains about 75 to 750 mers in rubber and plastics, hence their DOP is 75 to 750. The average molecular weight is up to 10000 in rubber and up to 100000 in plastics.
Mechanism of Polymerization
In the formation of long chain polymers, various monomers join themselves together. They will join each other only when the molecules are available at the ends of a chain. It therefore, desires that the sites for polymerization reaction should exist in each nonomer.
These reaction sites may be bi-functional, tri-functional, tetra-functional if the available reaction sites are two, three and four respectively. The polymerization process in ethylene is bi-functional.
The following mechanisms are involved in various polymerization processes.
- Addition polymerization
- Copolymerization
- Condensation polymerization
Addition Polymerization
When two or more chemically similar monomers are polymerized to form a long molecular chain, the process is called addition polymerization.
The process involves a catalyst i.e. an initiator besides suitable temperature and pressure. Polyetheylene is produced by this process.
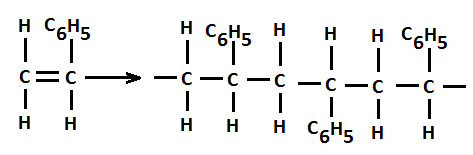
For example, additional polymerization of styrene results in a product called polystrene. It is shown in above Figure 2.
Copolymerization
When two or more different monomers are polymerized to form a long molicular chain, the process is called Copolymerization. This process may be visualized as a special type of addition polymerization.
Butadiene-styrene and vinylchloride-vinylacetate are examples of copolymers.
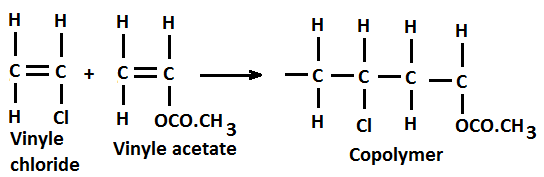
Above Figure 3 shows formation of copolymer from monomers of vinylchloride and vinylacetate. Double covellent bonded carbon atoms in these monomers are broken and single bonds are formed. A new kind of vinylchloride-vinylacetate molecule forms during the process. Copolymerization process is used in the manufacture of synthetic rubbers.
Random addition of two monomers form a random copolymer while their ordered addition results in block copolymer. Styrene butadiene rubber is example of it. By changing the sequence of different monomers, different varities of copolymers can be obtained.
Condensation Polymerization
The process in which two or more chemically different monomers are polymerized to form a cross-link polymer, along with a by-product such as water or ammonia, is known as condensation polymerization. It takes place in unsaturated organic compounds.
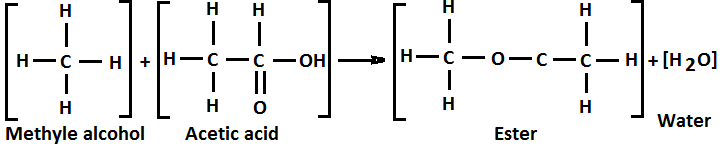
Above Figure 4 shows how methyl alcohol (CH3OH) and acetic acid (CH3COOH) condense to form a long chain polymer called ester along with water as a by-product.
Cross-linked polymers: In addition to chain polymers, three dimensional network polymers can also be formed. Such polymers are known as cross-linked polymers.
For example, cross-linking of monomers of formaldehyde (HCHO) and phenol (C6H5OH) gives a polymer named phenol formaldehyde and water as by-product. Phenol formaldehyde is also known as bakelite and is used in making gears of automobiles. Some commercial plastics made by condensation process are given below.
Commercial name | Product of condensation process |
Durez | Phenol and formaldehyde |
Glyptol | Phthalic acid and ethylene glycol |
Mylar (film) | Phthalic acid and ethylene glycol |
Melmac | Melamine and formaldehyde |
Texalite | Phenol and formaldehyde |
Additives in Polymers
Additives are the substances mixed with monomers to obtain desired properties in polymers. This addition is done prior to or during the polymerization process. Additives usually added to the monomers are given below.
Additive | Example |
Plasticizers | Tricresyl phosphate, camphor, resins, organic solvents. |
Fillers | Mica, asbestos, wood, slate powder, glass powder. |
Catalysts (i.e accelerators, or hardeners) | Solid form: benzoyl peroxide with calcium phosphate and camphor Paste form: benzoyl peroxide with tricrecyl phosphate Liquid form: acetyl peroxide, dimethyl phthalate. |
Initiators | Hydrogen peroxide (H2O2) |
Dyes and Pigments | Metallic oxides |
One or more of these are added in varying proportions. Their characteristics, properties and important applications are described below.
Plasticizers
- These are organic compounds of low molecular weight.
- They are oily in nature.
- Plasticizers act as lubricants and improve the flow of material during processing.
- These impart flexibility and toughness to the materials.
- They prevent crystallization (i.e. maintain noncrystalline structure) by keeping the chains separated from one another.
- They impart flexible nature to the thermoplasts.
- P.V.C., hard at room temperature, is plasticized with tricresyl phosphate to make it flexible.
- Synthetic celluloid made from nitrocellulose is plasticized with camphor.
Fillers: Addition of fillers improves heat resistance, strength, and dimensional stability.
Catalysts: The rate of polymerization reaction is increased due to their addition.
Initiators: Their addition help to initiate the polymerization process. They also stabilize the reaction sites in molecular chains.
Dyes and Pigments: Their addition is optional, and is needed to impart desired color to the materials. Red, blue, green and other color shades may be given to the polymers by addition of dyes and pigments.
Deformation of Polymers
Deformation of polymers is affected by their structural configurations. As the attractive forces between adjacent molecules is small, permanent deformation takes place due to slip between the adjacent molecules. Deformation of all aligned linear molecules is shown in Figure 5(a) below.
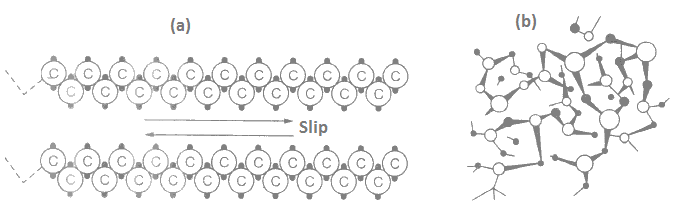
Here the deformation by slip occurs at the weaker regions between the molecules. A noteworthy point here is that intermolecular bonds do not break during deformation. Plastics deform easily under pressure and high temperatures.
Above Figure 5(b) shows a three dimensional structural arrangement of phenol formaldehyde. Here a continuous structural framework exists, therefore slip cannot take place between the molecules.
Infact the primary covalent bonds exist throughout the structure. This type of polymerized plastic is known as thermosetting plastics and makes a permanent set.
Types of Plastics
Long chain polymers are sub-grouped into three types.
- Plastics (isotropic in nature)
- Fibers (directional in nature)
- Elastomers (rubber-like elastic nature)
Here, we will discuss about plastics. Plastics is the name given to a material which is a mixture of resin, catalyst, accelerator, inhibitor and pigment.
Resin forms a major part of this mixture and hence the properties of plastics are mostly governed by the properties of the resin used. Plastics are broadly classified into two categories.
- Thermosetting (or thermoset), and
- Thermoplastic (or thermoplast).
They differ from each other in the way in which they are affected by heat.
Thermosetting Plastics
They have a three-dimensional network of primary bonds in all the directions. These type of plastics, on application of heat, first become soft and then hard; after that they cannot be softened again by application of heat. This permanent hardening called curing is a chemical change.
They generally require both heat and pressure to be molded into any shape. If intensly heated they breakdown by degradation. Common examples of themosets are phenolics, epoxies, melamine, bakelite DAP etc.
Thermoplastics
Their long chain molecules are secondary bonded which break more rapidily due to increase in thermal energy. They become soft, when heated (generally with pressure) but require cooling to set into a definite shape.
Since no chemical hardening action take place, the shaped articles re-soften on reheating. Only a physical change is involved with them. They have excellent plasticity but low melting point. Common examples are cellulose, nylon, polyvinylchloride, teflon etc.
Thermosets | Thermoplasts | Comparison
Thermosets are non-recycleable plastics but thermoplasts can be recycled again and again. Their characteristics and properties are compared below.
Description | Thermosets | Thermoplasts |
Bonding network | 3-dimensional, primary in all directions | Chain molecules are secondary bonded |
Effect of heat | Becomes hard and cannot be soften again | Bond breaks and becomes soft |
Consequence of curing | A chemical change occurs during permanent hardening | No chemical change occurs |
Mouldability to any shape | Both heat and pressure are required | Requires cooling for setting |
Effect of intense heating | They breakdown by degradation | They resoften |
Melting point | They do not melt | 116°C – 330°C |
Normal usable temperature | 80°C – 300°C | 60°C – 200°C |
Mechanical Properties of Plastics
Plastics are characterized by the following mechanical properties.
Strength: They have low tensile strength. Their strength in compression is better than in tension. Tensile strength of thermoplasts generally ranges between 15 to 90 MPa.
High temperature suitability: They have low melting point, therefore are unsuitable for high temperature usage, generally above 100°C. Dimensional stability is poor due to creep effect at room temperature. At higher temperatures, this is poorer due to softening in them.
Weather effect: They are susceptible to weather conditions. They suffer from distortions in moist conditions, and are highly affected by chemical (acidic and alkaline) environments.
Fatigue failure: They have poor resistance to fatigue failure, and generally fail at much lower stresses as compared to their yield strength. They do not exhibit endurance stress, therefore they are designed for a certain estimated number of cycles of failure.
Stress-strain profile: Some plastics are linearly elastic but most of them arc non-linearly elastic. Therefore, their stress-strain profile is of mixed variety.
Crack formation behaviour: They fail due to formation of cracks in the regions of localized stress concentration (e.g. notches, sharp flaws, scratches etc.). It happens due to breaking of covalent bond in the network.
Fracture mode: The thermosetting plastics fails in brittle mode but the thermoplasts can fail in both: the ductile, brittle, or ductile-brittle transition mode.
Thermal and Electrical conductivity: They are poor conductors of heat and electricity. Therefore, they are used as insulators also. Bakelite, pvc, resins, plastic films etc. are used for these purposes.
Impact strength is low which further decreases at higher temperatures due to softening.
Hardness is lower than those of metals and ceramics. It is generally between 5 to 30 BHN which is comparable with hardness of talc and lead alloys.
Tear strength is moderate. It is defined as the ability to resist tearing, especially or thin films used in packaging. The magnitude of tear strength is related with the magnitude of tensile strength.
Processing of Plastics
Quite a number of techniques are employed for processing of plastics to make large variety of components. The kind of method used depends upon whether the plastic is thermoset or thennoplast, the softening temperature of thermoplast, geometry and size of the finished product.
Moulding is the most common method for forming plastics. Following moulding techniques are generally employed for this purpose.
- Compression moulding – which suits more for thermosets.
- Transfer moulding – which suits more for thermosets and pieces having complex geometries.
- Injection moulding – is widely used with thermosplasts.
- Extrusion – is used with thermoplasts to produce tubes, rods, sheets, filaments etc.
- Blow moulding – is used to form containers, bottles, toys etc.
.
Besides moulding, some other techniques are also used to process the plastics. These are:
- Calendering (or sheet forming) – which is suitable for manufacturing floor tiles and sheets etc. (i) Thermoforming (ii) Laminating and reinforcement
- Casting – which is suitable for both thermoset and thermoplast
Compression Moulding
This process consists of placing a specific amount of polymer in a the-cavity, which is then squeezed by a punch. The plastic material is heated in most of the cases to a temperature ranging from 125°C to 260°C which softens the material. Thus the material fills the cavity when sufficient pressure (about 3.5 to 40 MPa) is applied on it.
Compression moulding is usually used for thermosetting plastics. For that the mould is kept closed for enough time to complete chemical reaction (or polymerisation) and thus the material hardens. Heat for curing is supplied through the walls of the die which is also heated to reasonably high temperatures. Curing time can be reduced to as low as 50% if so desired, by preheating the charge.
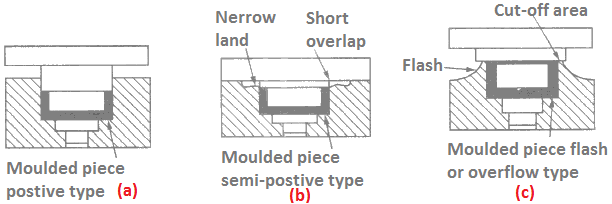
Arrangements of compression moulding are shown in above Figure 6(a, b, c). These arrangements depict three different styles of compression moulding viz. (i) positive type (ii) semi-positive type (iii) flash (or overflow) type.
In positive type full pressure is exerted to make the material to fill the mould, in semi-positive type full pressure is exerted at final closing of the mould, and in flash type the excessive material can flow-out of the cavity in the form of thin flash.
Amongst these, the positive type is preferred to produce accurate parts since the amount of charge material can be controlled precisely. Semi-positive type is used to produce quality product in a large quantity, while the flash type is used for producing any kind of product. This method is cheap also since it does not require any precise control over the charge. However, each piece has to be trimmed to get the dimensional accuracy.
Transfer Moulding
In this method as shown in Figure 7 below. The charge material is heated to fluid form and then compressed in a closed chamber. Consequently, the molten plastic is forced into the closed mould cavity through a sprue runner.
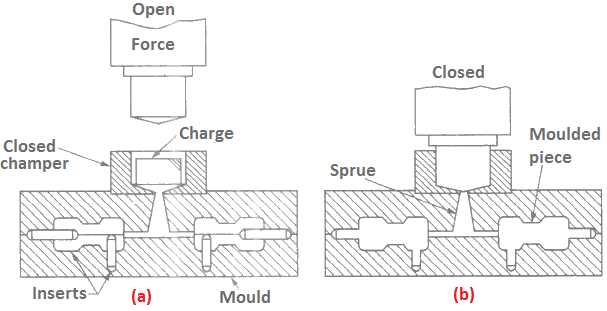
On solidification, the plastic acquires the shape as provided in the mould. The inserts are provided in the mould to help in easing out the solidified product.
Although the preparation of mould involves a high cost, it produces the products of uniform density and closer tolerances. And also since the applied pressure is of higher intensity, a greater strength is possible in the products. This process is used to produce plastic products on mass scale.
Injection Moulding
Depending upon the type of machine used, several techniques are employed for injection moulding. These are:
- single-stage plunger type injection moulding,
- single-stage reciprocating screw type injection moulding, and
- two-stage plunger (or screw) plasticiser type injection moulding.
Whatever may be the type of machine used, basically an injection moulding machine heats the material to its softened state, injects the soften material into die-mould, which is then cooled to harden a thermoplastic material.
Operating temperatures vary between 150°C – 370°C and full pressure may vary between 35 – 350 MPa. The moulds are watercooled, the product solidifies quickly, and is then ejected by knockout pins.
Injection moulding provides the highest rate of production, thereby a low production cost. It can easily accomplish 300 to 400 shots per hour. A single-stage reciprocating screw-type machine is shown in Figure 8(a) and a two-stage plunger (or screw) plasticiser type in Figure 8(b).
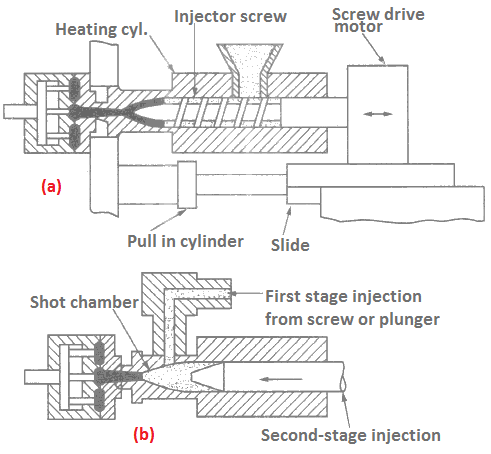
The single-stage reciprocating screw machine consists of a screw which turns and starts crushing the charge falling from a hopper. The charge fills into the heating chamber where mixing and crushing takes place by the screw. When sufficient material is prepared, the screw stops working and now it starts working as plunger. The plunger drives the charge forward into the die. Since the mould is of spliting type, the product can be taken out easily.
Another method of two-stage injection moulding consists of two stages. In the first stage the charge material is plasticised in one cylinder and a definite amount of charge is transferred into shot chamber by screw plunger. In the second stage a simple plunger takes the softened charge from the shot chamber into the die mould, and injects it.
Extrusion
In this process a continuous flow of material is provided to a die. A large variety of plastics are extruded into long shapes by forcing them through a die with the help of screw. This process is accomplished with the help of a plunger into a cylinder.
This process consists of a hopper through which the charge material in the form of powder/pallets is fed to a heated chamber. The heated cylinder carries a screw feeding mechanism, a nozzle and die-assembly. The screw mechanism while rotating inside the cylinder, carries the heated charge (soft charge) forward and forces it through a heated die-assembly continuously.
The die-opening controls the required shape. As the product leaves the die, it is being cooled and carried on a conveyor arrangement.
This process is very rapid and more economical as compared to other processes. It gives a very high production rate. It is capable to produce complicated/complex shapes without any difficulty. Thermoplastics, thermosetting plastics and elastomers can be easily worked by this process.
Blow Moulding
This process is similar to the glass forming blowing process described earlier. It is used to make products of hollow geometry such as plastic containers etc. During forming, a length of plastic tubing (also called parison) is extruded first.
While in semi-molten state, this is placed in a two-piece mould whose configuration conforms to the shape of container to be produced. Then the air or steam is blown under pressure to form the hollow cavity. For accuracy of shape and size of the product, the temperature and viscosity of parison has to be regulated carefully.
Calendering (Sheet-Forming)
It is an important process for manufacturing plastic sheets. In this process plastic material which is composed of resin, filler, plasticizer and colour pigment is allowed to pass through a series of hot rollers known as sheeting rolls. As the plastic compound is squeezed between the rolls, a product emerges in the form of sheet.
Thickness of the sheet can be controlled by varying the distance between centers of rolls and by changing the speed of finishing rolls. The finished product (sheet) is then taken up on a roll after passing over the water-cooled rolls. Water-cooled rolls help to cool down the sheet.
Commercially, vinyl floor tiles, acetate sheeting etc. are made by this process. These sheets can further be converted into other shapes as discussed below.
Thermoforming: This process is used for shaping hot sheets of thermoplastics into a large variety of thin walled articles such as display packages, bowls, trays, refrigerator door liners etc. For that the thermoplastic sheet is softened and is held in desired shape until it cools and becomes solid.
This process may also be performed by pressing the sheets under a bending machine. The bowls and trays can also be manufactured from these Sheets by blowing or drawing them under air-pressure or vacuum against a mould.
One of the biggest advantage of sheet forming is its ability to convert the sheets into decorative articles. Later, these articles can be coated or printed in the form of metallic finish, wood grain finish etc. This process is very economical and can give a high production rate. These sheets have an extensive use in industries, buildings, houses etc. also.
Laminating and Reinforcement: Sheets and rods etc. can also be produced by laminating the materials impregnated with plastic resin. Most of the laminated sheets consist of sheets of wood, asbestos, fabric and other materials coated by resin and then processed by applying heat and pressure.
Reinforcement materials generally include paper, cotton, asbestos, nylon etc. and the impregnating resins are phenolics, silicones etc. These are compressed under a pressure of about 70 MPa at 150°C to harden the resin.
Casting
Plastic products can also be formed by casting process which is similar to casting of metals and ceramics. For that the molten plastic has to be poured into a mould and allowed to solidify. The contour of the mould needs to match with geometry of desired product. Casting can be done for both: the thermosets and thermoplasts.
The thermoplasts solidify on complete cooling, but in thermosets the hardening is achieved by curing at high temperature. Plastics formed by casting process are called ‘cast plastics’. They find use in consumer goods, automobile items etc.
Thermal Behaviour of Polymers
The alternation in the behaviour of polymers over a range of temperature is of practical significance to a material scientist. The variation of elastic modulus E with temperature for polystyrene is shown in Figure 9 which is a typical profile of polymers in general. It shows five different regions from which the polymer passes through during temperature variation.
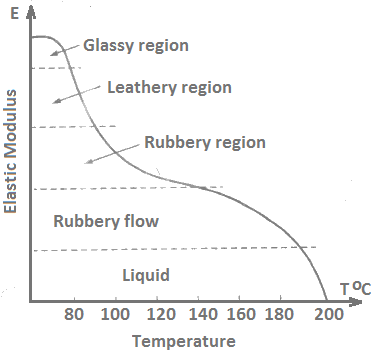
In the glassy region (up to 80°C), a polymer is hard and brittle. In this region, strain occurs by stretching of bonds within and between molecular chains. The behavior of polymers in this region resembles like the deformation of a spring.
In the leathery region, the modulus drops rapidly with increasing temperature. Reversible sliding becomes possible in the chain as the small sections move causing neighboring sections to move.
In the rubbery region, viscoelastic behavior of polymer dominates deformation. As the temperature increases above the glass-transition temperature Tg, the molecular segments slide reversibly past one another and tend to strengthen out.
In the rubbery flow and liquid regions, permanent sliding molecules dominate the deformation process. As temperature increases, the viscosity decreases and at high temperatures the polymer is essentially a liquid.
The rubbery region is absent in a crystalline polymer. The elastic modulus in such a material decreases gradually with increasing temperature until the melting point is reached. Most polymers contain both crystalline and amorphous regions. Elastic modulus versus temperature curve of crystalline, cross-linked and non-crystalline polymers is shown in Figure 10. It is highest in crystalline polymer at all temperatures.
Glass-Transition Temperature
The transition from glassy to rubbery behavior in non-crystalline polymers appears in modulus-temperature plot. Figure 10 shows a break in the slope of this curve at the glass transition temperature Tg.
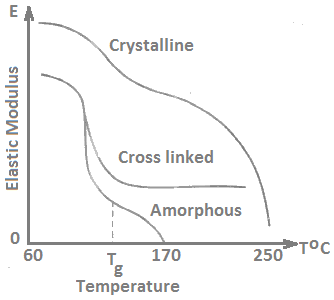
It marks the point above which molecular segments are free to move past one another, and below which they are confined. At temperatures above the glass transition but below the melting point, the crystalline polymers are rigid and non-brittle.
The glass-transition generally occurs at temperatures between 0.5 to 0.65 Tm where Tm is the absolute melting point in kelvin. Glass-transition, softening and melting temperatures of some polymers are shown Table below.
Polymer | Glass-transition temperature (oC) | Softening temperature (oC) | Melting point (oC) |
Polyethylene | – 78 | 50 | 140 |
Epoxy | 50 – 200 | 200 | Do not melt |
Polyester | 50 – 200 | 150 | Do not melt |
PMMA | 100 | – | – |
Polystyrene | 90 | – | 235 |
ABS | 70 – 110 | – | – |
Polypropylene | – 10 | – | 0 |
PVC | 87 | – | 212 |
Polycarbonate | 160 | 135 | 270 |
Nylon 6 | – | 60 | 225 |
Polymides | – | 400 | 377 |
Future of Plastics
Plastics are assuming new dimensions in their development and applications. Newer kind of plastics having properties and characteristics comparable to metals have emerged. Polyurethanes, polyacrelates are used as shape memory polymers; and polypyrrole as chemically responding polymers are the most recent developments. Some special purpose plastics are described below.
Expanding Plastics
Common plastics shrink when cured. Expanding monomers (EMs) experience zero shrinkage during polymerization. The polycyclic ring opening monomers are combined with conventional monomers and oligomers to produce expanding plastics.
These plastics have enhanced resistance to corrosion and abrasion. Expanding monomers find use in coatings, adhesives, dentistry, medical prostheses, electronics and other industries. EMs may be used to
- eliminate internal stresses by expanding into microcracks in advanced composites.
- copolymerize with epoxies, acrylics, and urethanes to generate unprecedented properties in aviation and aerospace plastics applications.
- deliver bio-degradable polymerized vesicles in Pharmaceuticals.
- produce advanced microchip sealants, and conductive links in electronics.
- combine with GMA for superior fillings, dentures, and crowns in dentistry.
Conducting Polymers
The advent of polyacetylene (PAC) in early seventies raised hopes and interest in conducting polymers. This system, however, is non-conducting, and maybe regarded as semiconducting.
The conducting fillers such as metals wires and powders, graphite powders and transition metal compounds are incorporated in non-conducting polymers to make them conducting.
Advancement: In a later development the conductivity of PAC is enhanced by more than ten times when iodine is doped into it. The doped PAC possesses conductivity much higher, and almost equal to metallic range.
It, however, loses conductivity rapidly when exposed to atmospheric conditions. Another limitation is the migration and loss of dopant from the surface.
Uses: Conducting polymers can generate electric signals by ion-exchange mechanism. Conducting electroactive polymers belong to the class of smart materials and are used as chemical sensors.
Polymers in Electronics
Several polymers show excellent opto-electronic properties. Many polyimides are used for Integrated insulation and cross overs for microwave integrated circuits. Aviation radome, anti-radar paints, and heat shields are some novel applications of special polymers.
Liquid Crystal Polymers (LCP)
These are made of rigid, rod-type, ordered molecules, which maintain their crystalline order even on melting. Based on the molecular orientation displayed, they are classified as follows.
- Nematic liquid crystal polymers, and
- Symectic liquid crystal polymers.
The main difference between these polymers, and the conventional liquid crystals used in electrical display devices, is their molecular weight. LCPs have much higher molecular weight.
Types of LCPs Advantages: Depending on packing arrangement of rigid units, there are two types of LCPs.
- Main chain LCPs (e.g. polyesters, polyamides), and
- Side chain LCPs (e.g. polyacrylate, polymethacrylate, poly-siloxane).
The advantages of these polymers over conventional plastics are their high impact strength, excellent dimensional stability, low thermal expansion, better chemical resistance, and outstanding processability.
They are used in highly specialised areas viz. telecommunication, fibre optics, chemical and hostile environments. Xydar and Vectra are commercial LCPs developed in 1984.
Photocurable Polymers
These polymers find applications in microlithography for making printing plates, photoresist for microcircuits, video discs and optical fibre coatings etc.
In this highly specialized radiation curable system the photoresist such as polyvinyl cinammate and related materials are synthesized by using low temperature interfacial transfer catalysed technique.
Biomedical Polymers
Medical and pharmaceutical applications of synthetic polymers range from
- catheters to vascular grafts,
- from semiocclusive dressings to mammary implants, and
- from transdermal drug delivery systems to medicated patches.
Current activities of device designers, manufacturers and research physicians indicate that devices manufactured from synthetic polymers are being increasingly accepted as the biomaterial of choice in most applications requiring compliance with soft tissue, cardiovascular tissue, or being non-irritating to the skin for transdermal applications.
Desired characteristics: The biomedical polymers should be such that the blood, enzymes and proteins should not cause adverse immune response, cancer, toxic and allergic reaction.
Highly crystalline polymers such as nylon, polyethylene, polyurethane and protein are used after testing and treating for creep, stiffening, stress and strain etc.
Silastic rubber, teflon, siloxane-urethane polymers, surface modified elastomers by hydrogels, glass reinforced plastics (GRP) composites etc. seem promising materials.
Applications: A few selected biomaterials in blood contacting applications are as under:
- Segmented polyurethane, polydimethyl siloxane and segmented copolydimethyl is used for artificial heart, heart valve, vascular tubing.
- Siloxane-methane, perfluorobutyryl ethyl, cellulose and polyallyl sulfone is used as membrane in oxygenator.
- Hydrogels is used as grafted surface for polymers.
Polymer Foams
The development of technology, especially in the aviation and building industries, created stringent requirements that could not be met by existing natural and manmade materials. Research began in the late 1930s and early 1940s in many countries with the aim of creating new gas-filled materials based on synthetic organic compounds.
At present hundreds of various elastic and rigid gas-filled materials such as nomex honeycomb, polyurethane are used in literally all branches of industry and produced on the basis of reactive oligomers and high polymers. Production of these materials is rapidly expanding at an exceptional rate.
The current technology for processing and production of foamed polymers, including thermosetting and thermoplastic polymers such as polyolefins, polyvinyl chloride (PVC), polyurethanes, structural foams, and filled and reinforced foams (syntactic) are much advanced.