Chemical Heat Treatment Processes
In this article I will discuss chemical heat treatment processes. (All other heat treatment processes are discussed in the previous post. This article is next part of that. So for batter understanding, also read that article.) These are:
1. Case Hardening Process (or carburising)
- solid or pack carburising
- liquid carburising, and
- gaseous carburizing.
2. Cyniding
3. Nitriding
4. Carbo-nitriding
5. Flame hardening
6. Induction hardening
Case Hardening Process
This is a method of producing steel having tough inner core and hard outer surfaces. Components such as gears, pins, pistons and camshafts are hardened by this process. Case hardened steel is capable of absorbing shock loads as well as resisting wear and abrasion. This process involves heating of steel in contact with a carbon-rich substance above critical temperatures for a prolonged duration.
In due course (the duration may vary between hours to days), the carbon penetrates into the steel to form a solid solution on the outer surfaces. Mild steel can be converted into a high carbon steel with addition of desired amount of carbon.
Types of Case Hardening Process
On the basis of carbon-rich substance used, the case hardening process of steel can be classified into the following types.
- Solid or pack carburizing,
- Liquid carburizing, and
- Gaseous carburizing.
Pack carburizing: In this process, a solid substance such as coke, coal, charcoal, carbon black, carbonates of barium, calcium or sodium is used. The steel object is cleaned and placed in a closed chamber amidst the surrounding of solid fumes.
This chamber is heated to a desired temperature for a long duration. Carbon gets soaked into the surface of steel. The depth of soaking depends on the time of exposure between steel and the solid fumes. Normally 0.1 mm penetration (soaking)) takes place in an hour. This method suffers from scale formation at the surface of the object.
Liquid carburizing: In this case, a liquid hydrocarbon rich in carbon is used either in a bath or by a pressure system. The heated steel is impinged upon by jets of liquid rushing out of nozzles. In due course of time, carbon gets deposited on the steel.
The steel is heated by gas burners or by electrical means. A case depth of 0.1 mm to 0.5 mm can be suitably obtained by this method. This method is better and faster than pack carburizing. Scaling of the object is also not a problem.
Gas carburizing: In this process, the component is heated in a furnace whose surrounding is filled with carbon-rich gas such as methane, propane etc. The hydrocarbons in carburizing gas decompose at high temperature, and the carbon gets deposited on the steel surface. The thickness of hardened case depends on the rate of gas flow. Small components such as ball and roller bearings, pins and axles can be case hardened suitably.
Cyaniding
This is a special case hardening process in which the mild steel absorbs carbon and nitrogen to obtain a hard surface. The component to be case hardened is immersed in a bath of sodium cyanide (NaCN) at about 400°C. It remains clipped in the bath until soaking takes place to a predetermined depth.
The component is then quenched in oil or water to obtain a hard surface. A case depth of 0.1 mm to 1.0 mm may be produced by this process. The hardened case contains about 4 to 4.5% carbon and 0.5 to 4% nitrogen.
Cyniding increases the fatigue limit of steel. This process is costly but less time consuming. Distortions in cynided components are also less.
Nitriding
This process involves heating of steel to about 650°C, and holding it there in the atmosphere of ammonia (NH3) for some time. The nitrogen from ammonia penetrates into the surface of steel, and forms very hard nitrides on the surface. These nitrides then disperse inside the steel. Hardness of about 1000 BHN may be achieved on 0.7 mm case in 100 hours by this process.
Salient features: Salient features of nitriding are as follows.
- It improves corrosion resistance.
- It provides very high hardness.
- Components need not to be machined after the process.
- Any other heat treatment is not required to be done.
- Scale formation does not occur.
- Cracks and distortions are almost absent.
- It is costly and time consuming process.
Nitriding is performed on dies, mandrels, gauges, parts of pumps and internal combustion engines.
Carbo-nitriding of Steel
In this process, the carbon and nitrogen are simultaneously introduced on the surface of steel by heating it between 650°C to 950°C in an atmosphere of anhydrous ammonia and carburizing gases. Thereafter, it is quenched in a suitable medium.
By doing so, the nitrogen gets concentrated near the surface and is backed up by a carburized case. However if enough nitrogen is present, a very hard surface is obtained even without quenching. The surface hardness obtained by this method is higher than that obtained in carburizing process.
Generally, medium carbon steels are carbo-nitrided by this process to a case depth up to 0.6 mm for applications which do not involve heavy shock loads. Case depth up to 0.25 mm is usually used for light duty applications.
Flame Hardening
In this process, the component is heated above critical temperatures in a local region by oxy-acetylene flame, and simultaneously quenched by spraying water under pressure, as shown in Figure.
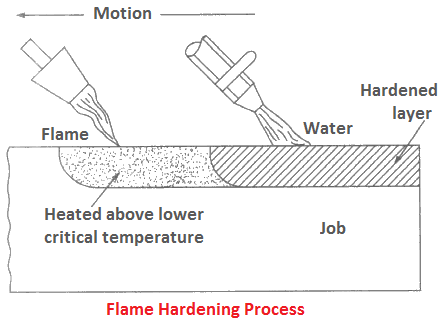
The depth of hardened case depends on the temperature of the flame, its heating time, temperature of the cooling water, and time elapsed between heating and cooling of a certain region.
This process is used for local hardening of components such as a gear tooth or few teeth, part of a wheel, and cutting tools. The process is cheap and its equipments are portable.
Induction Hardening
By this process, we can get a hard and wear resistant surface with a soft core in steel. The process involves induction heating whose schematic arrangement is shown in Figure.
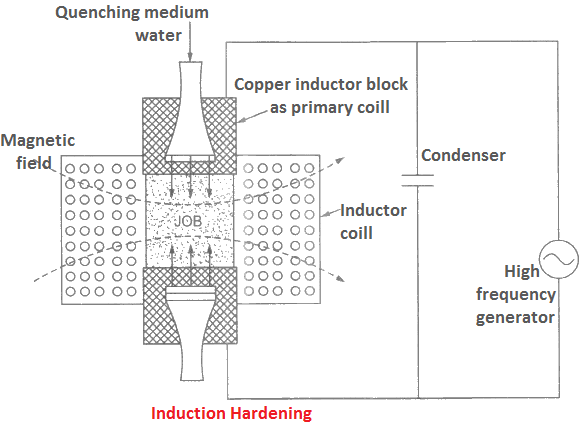
The job to be hardened is placed in an inductor coil that comprises of several turns of copper tube. A high frequency current of about 1000 to 10000 cycles per second is passed through a copper block which acts as primary coil of transformer.
This sets up an alternating magnetic field, and induces an alternating current. This current produces heating effect on the job’s surface. Temperature produced is about 750 to 800°C. The heated surface is simultaneously quenched by a spray of water.
Induction hardening is a rapid process. Hardness to a depth of about 0.8 mm can be achieved within a few seconds. The actual time taken depends on the power input, depth of hardening and frequency of current. Advantages this process are as under:
- Depth of the hardness can be controlled by controlling the voltage and current.
- As the process is very rapid, hence it is suitable for mass production.
- Warpage and deformation is the least.
- Scale formation does not occur.
Induction hardening is a suitable heat treatment process for camshafts, crankshafts, gears and various automobile parts.
Jominy End-quenched Test
It is a method of determining hardenability. Hardenability is defined as the ability of steel to get hardened by any process, such as martensitic transformation, sudden quenching, spray cooling or any other means.
All materials do not show equal hardenability. The hardenability of heat treated steel can be measured by end-quench test suggested by Jominy.
A cylindrical bar 100 mm long and of 25 mm diameter is used in this test. The test-piece is heated and held above 1100°C so that a uniform austenitic structure is formed. It is then quenched by water until it reaches room temperature. The hardness is measured at an interval of 1.5 mm from the quenched end.
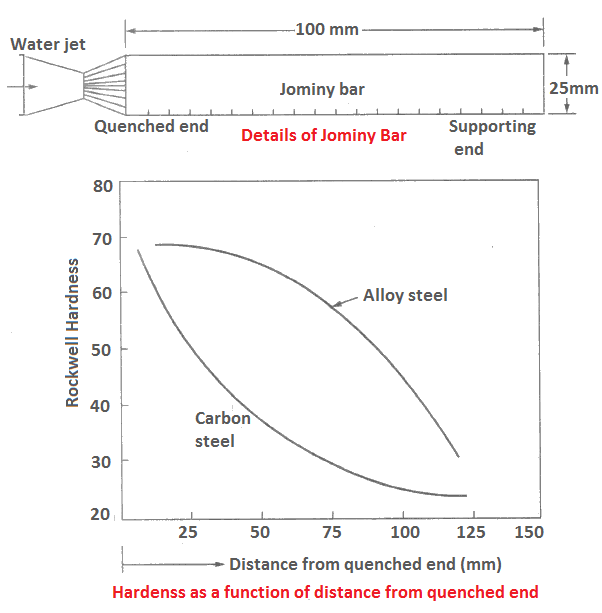
Figure shows the arrangement of the test set-up. Rockwell hardness for plain carbon steel and alloy steel as a function of distance from quenched end is also shown.
Variables affecting the hardenability of steel and alloy steels: Since the hardenability is a measure of depth to which a ferrous metal and alloy may be hardened by formation of martensite upon quenching from a temperature above the upper critical temperature.
It is mainly affected by the factors involved with heat treatment, micro-constituents of transformation and the material’s composition. Thus the hardenability of steel is influenced by the following variables:
- rate of cooling,
- carbon content,
- quenching rate,
- quenching medium,
- type of microconstituent formed during cooling and/or quenching nature of the alloying elements in case of steel alloys,
- style of cooling: whether spray cooling or cooling by dipping in a liquid bath,
- sub-zero treatment, etc.
Strengthennig Mechanism
To meet the challenges of advanced technologies, new materials are needed to be developed. The new and conventional materials desire their strengthening and hardening so as to withstand varying functional conditions.
The behavior of a solid depends on its chemical composition, mechanical properties and thermal processing. Heat treatment, casting, hot-working, sintering etc. are the thermal processes that influence the mechanical properties by changing grain sizes and phases.
Accumulation of dislocations during plastic deformation also adds to the strength of a metal. Following are the various strengthening and hardening mechanisms:
- Cold working method
- Precipitation (or Age) hardening process
- Dispersion hardening process
- Solid-solution hardening method
- Grain size reduction method
- Strain hardening
- Martensitic transformation
- Some heat treatment processes
Although hot working is not a strengthening method, but it has been described with cold working for comparative understanding.
Hot and Cold Working Process
When the processes are carried-out below the recrystallization temperature (0.3TR, to 0.5TR ), these are known as cold working processes.
If the processes are performed above the recrysallization temperature, they are called hot working processes. Here Tm being the melting point in kelvin.
The two phenomena, cold working and hot working, are temperature related plastic deformations of metals. “Working” means processing or operations regarding fabrication of metals to some desired shapes. These processes may be rolling, forging, embossing etc.
The aluminum alloy torch body processed at room temperature, and the steel body of a car processed at about 200°C are the examples of cold working. While the fabrication of wheels of railway engines is an example of hot working. Let us elaborate it further.
The melting point of aluminum is 657°C (930 K) and that of steel in purest form is 1539°C (1812 K). The room temperature is taken as 27°C (300 K). The recrystallization temperature of aluminum is 0.5 x 930 = 465 K. Processing of aluminum at room temperature is a cold working process because 300 K < 465 K.
Similarly, recrystallization temperature of steel is 0.5 x 1539 = 770 K. Steel body of a car processed at 200°C (473 K) is lower than 770 K. Hence it is cold working process.
Contrary to this the fabrication of engine wheels carried-out at 800°C (1073 K) is higher than 770 K. Therefore it is a hot working process.
Cold Working Process
Following are the advantages and disadvantages of cold working process:
Advantages:
- increase in the hardness,
- increase in the yield and ultimate strengths,
- improved surface finish,
- closer dimensional tolerances.
Disadvantages:
- decrease in ductility,
- slight decrease in density,
- decrease in electrical conductivity,
- distortion in the microstructure of metals,
- formation of crystal defects (dislocations ),
- elongated grains in the direction of deformation,
- high mechanical energy required to cause plastic deformation,
- set-up of residual (or internal) stresses that remain within the metal unless removed by annealing or tempering processes, and
- raising of recryatallization temperature of metals.
Percentage of cold working: The amount of cold working (CW) is expressed as a percent of cold work. This indicates the percent reduction of thickness, or reduction in area of the metal. The percent cold working may be determined from following expressions:
%CW = (ta – td)100 ÷ ta
%CW = (Aa – Ad)100 ÷ Aa
Where ta and Aa are the initial thickness and cross-sectional area; td and Ad are the thickness and cross-sectional area after deformation respectively.
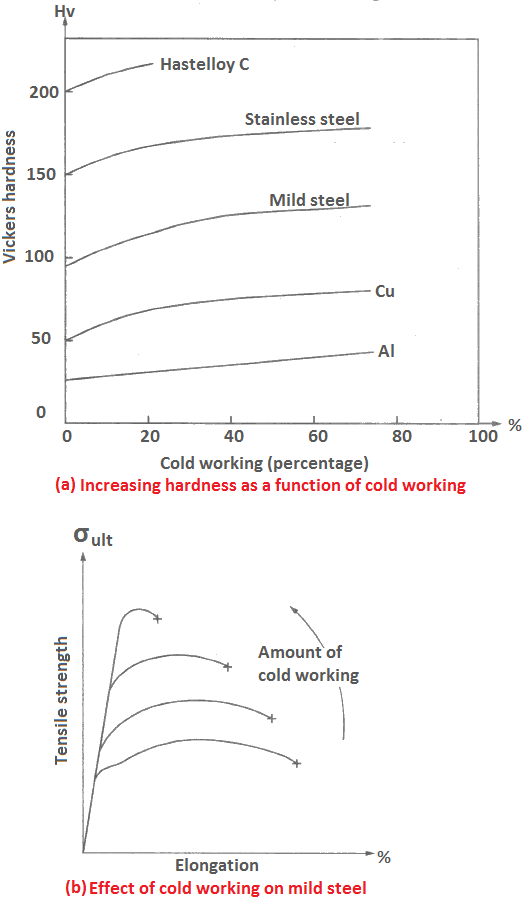
Effects of cold working: The effect of cold working on the hardness of some materials is shown in Figure (a). It indicates that the hardness increases with increasing cold working. Increase in tensile strength with a corresponding reduction in elongation due to enhancing amount of cold working in mild steel is depicted in Figure (b). The defects induced due to cold working may be removed or minimized by annealing, a heat treatment process.
Hot Working Process
This phenomenon may be regarded as a combination of cold working and annealing. A thermodynamic balance between induced deformation and the released strain hardening by high temperature is realized.
A high temperature may also mean room temperature for metals like tin and lead as their recrystallization temperatures are below the room temperature. Following are the some important observations related with hot working process:
Advantages:
- Density of metal increases due to disappearance of pores.
- Homogeneity of material improves.
- Fine grained structure is obtained.
- Change of shape of metal can be done easily and suitably.
- Large deformations are possible in hot working.
- The energy needed in deforming the metal is much less for hot working than the cold working.
- The ductility and toughness of the metal is improved.
Disadvantages:
- The loss of metal due to oxidation is considerable as hot working is normally carried-out in air.
- Reactive metals are severely embrittled by oxygen. Molybdenum is one such example.
- The cost of tools and handling equipments is high.
- The dimensional accuracy is less than that obtained from cold working.
- Good surface finish of the components is difficult to achieve.
Precipitation (or Age) Hardening
Some metals and alloys show increase in their hardness with lapse of time (i.e. after attaining certain age) at room temperature or after heating to a slightly higher temperature. This kind of hardening is called age or precipitation hardening. Precipitation hardening is an important strengthening method employed for metals not exhibiting allotropic transformation.
- Nonferrous metals and alloys such as magnesium and aluminum alloys, copper-beryllium alloys, and nickel base alloys use a solute element for their strengthening.
- Large volumes of the fine precipitate of solute element are uniformly distributed within the metal (and alloy) during the process.
- Precipitation in solid solution occurs when the solubility of solute decreases with decreasing temperature.
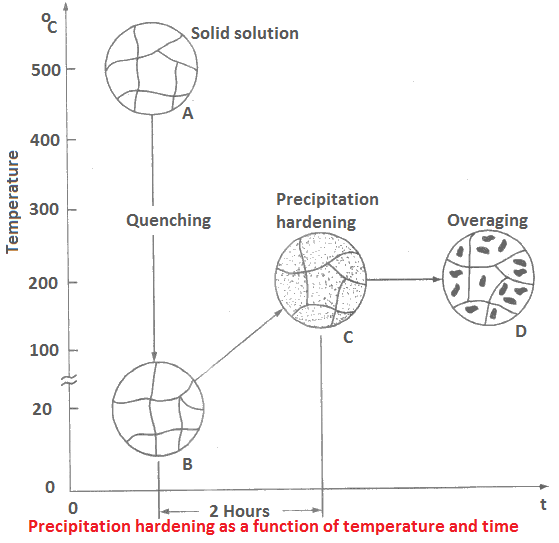
Figure depicts the process of precipitation hardening showing different stages sequentially from A to B, B to C and C to D. The data given are for Al-Cu alloy system with 4.5 % Cu.
- Stage AB is sudden quenching of a solid solution from 500°C to room temperature.
- Precipitation hardening shown by BC takes about 2 hours during which the crystal is heated to about 200°C.
- The effect of age hardening is shown at C, and that of overageing at D. The elongation decreases during ageing while yield and tensile strengths increase.
- These strengths decrease during overageing (CD stage) but the elongation remains constant.
Age hardening of steel: Steel is age hardened by keeping it at low temperature for hours. Carbon diffuses slowly and renders the steel hard. It is found that if the steel is kept at 20°C, it reaches to its maximum hardness in about 500 hours, whereas if it is kept at 80°C it reaches to its maximum hardness in about 10 hours only. Both, temperature and time are important factors during age hardening.
Special features:
- At lower temperatures, the precipitate particles become smaller. This results in greater strengthening effect.
- The precipitation-hardened alloys are not recommended for use above their solvus temperatures.
- Colored glasses, color filters, neon lamp tubes, rail signals, opaque glasses and the translucent glasses are produced by this process through proper distribution, composition and size of precipitating phases.
Dispersion Strengthening
The process involves dispersion of hard, ultrafine, thermally stable, and inert phase of metallic, intermetallic, or nonmetallic particles of less than 0.1 micron size in metal constituents.
- Generally the dispersion particles of carbides, oxides and borides are used.
- Shape of these particles may be round, disc or of needle type.
- Needle shaped particles provide maximum strengthening.
- Metals thus obtained are much stronger than pure metals and exhibit higher elastic limit.
Factors affecting strengthening: The extent of strengthening depends on the amount, characteristics, distribution, shape and size of dispersed particles.
- Too coarse or too fine particles have less strengthening and hardening effect.
- Average distance between two particles (i.e. inter-particle spacing l) depends on their size.
- For maximum strengthening, the value of l should be neither too less nor too much.
- Optimum properties are usually observed at particle concentration of 5% to 15% by volume.
These particles form effective obstacles against the movement of dislocations, resulting in increased strength. The distance between the dispersed particles must be small so as to provide hindrances to the dislocation movement.
Strengthening effect can be estimated by the shear yield stress ty required to move a dislocation of length l and Burgers vector b. Thus
ty = Gb ÷ l
Where G is shear modulus of the metal to be strengthened. The dislocation length and inter-particle spacing are of almost the same dimension.
Dispersion-hardening is more efficient than precipitation-hardening, especially at higher temperatures where age-hardening disappears. The oxide particles with negligible solubility prevent coarsening. Coarsening causes undesirable effect and reduces the strength of an alloy.
Non-occurrence of coarsening in dispersion hardening makes this strengthening mechanism superior to precipitation hardening in which coarsening causes loss of strength at elevated temperatures.
Solid Solution Hardening
Solid solution hardening (or solute-hardening) is an alloying process whose effectiveness depends on the size and percentage of the solute element. A solute atom larger than the solvent atom introduces a compressive strain field while a smaller solute atom set-up a tensile field.
This situation impedes dislocation motion, change in lattice constant and shear modulus in the immediate surroundings of the atom.
The yield strength increases by increasing percentage of soluble alloying element. It is highest in tin and lowest in zinc.
Recovery and Recrystallization
These are temperature dependent processes, generally performed on cold worked metals. The internal stresses are released in recovery without any noticeable changes in the material, while drastic changes take place during recrystallization. Temperatures at which these processes occur are:
- Tm for recovery,
- 0.3 to 0.5Tm for recrystallization of metals, and
- 0.5 to 0.7 Tm for recrystallization of alloys.
Where, Tm is melting point in Kelvin.
Recovery (or stress-relieving anneal): The recovery process is adopted in boiler tubes, cartridge cases, and components made by welding, casting and forging operations. This process is also known as stress-relieving anneal. During recovery, the following occurrences take place.
- Internal (residual) stresses are relieved.
- Structure becomes uniform.
- Increased dislocations during cold working are redistributed.
- Microstructure remains unaffected.
- Strength increases to a low extent, but there is no change in the mechanical properties.
Recrystallization: This process brings-up completely changed crystals at recrystallization temperatures which depend on the percentage of cold work. During recrystallization, the following changes take place in materials.
- Ductility of material improves.
- Tensile strength and hardness decreases.
- Distorted and elongated grains (crystals) formed due to cold working are restored.
- Higher degree of cold worked deformation lowers the recrystllization temperature.
- Pure metals recrystallize at lower temperatures.
The effect of cold working, recovery and recrystallization on different properties of materials are shown in Figure. The likely microstructural changes are also shown in this Figure. Recrystallization temperature may be raised-up by adding certain elements.
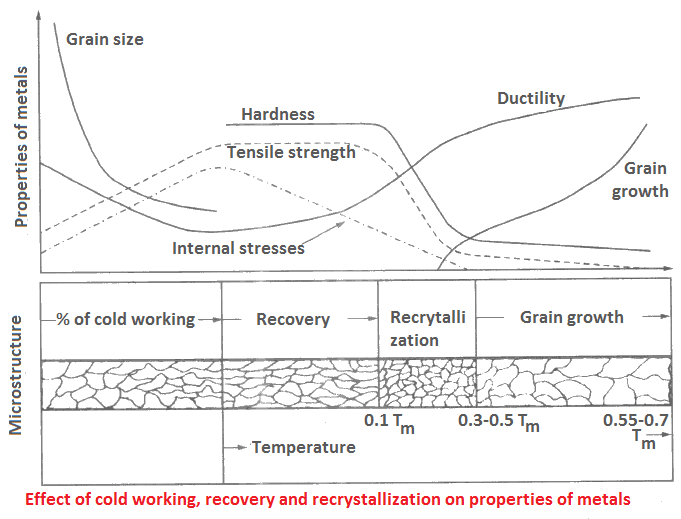