Aggregates for Bituminous Materials
Aggregates make up the bulk of bituminous materials; the percentage by weight ranges from about 92% for a surface course asphalt to about 96% for a dense, heavy-duty and high-modulus base asphalt concrete. The aggregate has important effects on the strength and stiffness of bituminous mixtures.
In asphalt concrete mixtures, the strength and resistance to deformation are largely determined by the aggregate grading, with the bitumen acting principally as an adhesive. Here the grading is continuous and provides a dense packing of particles, leading to a stable aggregate structure.
In hot rolled asphalt and stone mastic asphalt mixtures, aggregate grading is again important, but the properties are largely determined by the matrix of fines and bitumen. The majority of aggregates used in bituminous mixtures are obtained from natural sources, either sands and gravels or crushed rock. The main nonnatural aggregate source is slag, with blast furnace slag being the most commonly used. As with concrete, aggregates in bituminous mixtures are regarded as inert fillers.
However, whereas in concrete both the aggregate and the hardened cement paste are relatively stiff, in a bituminous mixture, the bitumen is very soft compared to the aggregate. Therefore the role of the aggregate in determining mixture stiffness and strength is more important in bituminous mixtures. Three size ranges are recognised in aggregates for bituminous mixtures. These are coarse, fine and filler. Coarse material is that retained on a 2-mm sieve, fine material passes 2 mm but is retained on the 63-micron sieve, and filler is material passing 63 microns.
Properties
The importance of grading has already been mentioned. In addition, aggregates suitable for use in bituminous mixtures must have sufficient strength to resist the action of rolling during construction. For surfacing materials, they must also be resistant to abrasion and polishing in order to provide a skid-resistant surface. Here the shape and surface texture of aggregate particles are important.
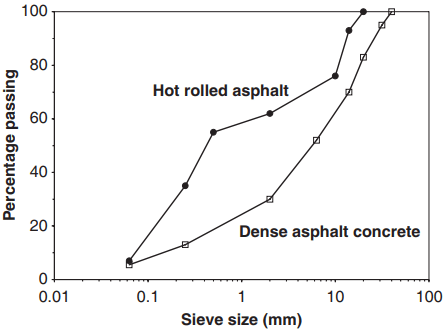
Figure 1 gives typical grading curves for a dense asphalt concrete (previously known as ‘macadam’) and a hot rolled asphalt (previously known as ‘asphalt’). The curve for the asphalt concrete clearly shows the continuous nature of the grading, whereas that for the hot rolled asphalt shows a gap grading with a lack of material in the range 500 microns to 10 mm. This is typical of a hot rolled asphalt, where the ‘mortar’ of fines and filler bound with bitumen characterises the material, the coarse aggregate providing the bulk.
The strength of aggregate is assessed in two ways. For resistance to crushing, the aggregate crushing value test is used. This test (BS 812: Part 110 and BS EN 1097-2) determines the extent to which an aggregate crushes when subjected to a steadily increasing load of up to 40 tonnes. The test sample consists of single-sized particles, 10–14 mm, and the amount of fines produced in the test is expressed as a percentage by weight of the original sample.
A variation of this test for weaker aggregates is the 10% fines test. Here the maximum crushing load that will produce 10% fines from the original singlesized sample is determined. The importance of this test is that it allows assessment of the extent of crushing that may occur during compaction. Resistance to impact loads is also required for road aggregates.
The impact value test (BS 812: Part 112 and BS EN 1097-2) determines the response of aggregate to blows from a heavy hammer. Once again the outcome of the test is the percentage of fines produced from the original single-sized sample. The skid resistance of a road surface is provided largely by the aggregate exposed at the surface.
There are two components, which are referred to as macrotexture and microtexture. The macrotexture is the overall road surface roughness, which arises from the extent to which there are spaces between aggregate particles. This is a function of mixture proportions. For example, a hot rolled asphalt provides an extremely low macrotexture because the coarse aggregate content is low and coarse particles are immersed in the fines/filler/bitumen mortar.
Consequently, a layer of single-sized aggregate particles is rolled into the surface to provide the required macrotexture. These are precoated with a film of bitumen to improve adhesion to the asphalt surface and are known as coated chippings. Asphalt concretes, on the other hand, have a lower proportion of fines and filler and provide a rough surface.
Macrotexture is measured in terms of texture depth using the sand patch test (BS EN 13036-1). The test involves spreading a known volume of sand in a circular patch over the road surface until it can be spread no further. The sand fills the spaces between aggregate particles as shown in Fig. 2. The diameter of the patch is measured and, knowing the volume of sand, the average depth can be calculated.

Microtexture refers to the surface texture of individual particles and varies according to the type of aggregate. Here it is important to use an aggregate which not only has a rough surface texture, but also will retain that texture under the action of traffic. This is assessed using the polished stone value test (BS 812: Part 114).
Here samples of aggregate are subjected to a simulated wear test, where a pneumatic tyre runs continuously over the aggregate particles under the abrasive action of emery powder. The skidding resistance of the samples is determined after the test using the pendulum skid tester.
Thanks for reading about “aggregates for bituminous materials”.